Polytetrafluoroethylene (PTFE) is a fluorinated synthetic polymer thermoplastic, most commonly known by the brand name Teflon. It is one of the engineering plastics used very widely in industrial applications. Due to PTFE’s chemical inertness, high melting point, and low coefficient of friction, rapid manufacturers often use PTFE to create custom parts in applications ranging from non-stick frying pans to medical devices to aerospace.
Despite its mediocre mechanical properties, it is one of the popular CNC machining and milling plastics for many specific applications.One of the best ways to manufacture Teflon parts is CNC machining. This article explores the ins and outs of Teflon processing: its material properties, processing advantages, common applications, and more. CNC machining PTFE is ideal for manufacturing parts for different applications that require good chemical resistance and high temperature stability.
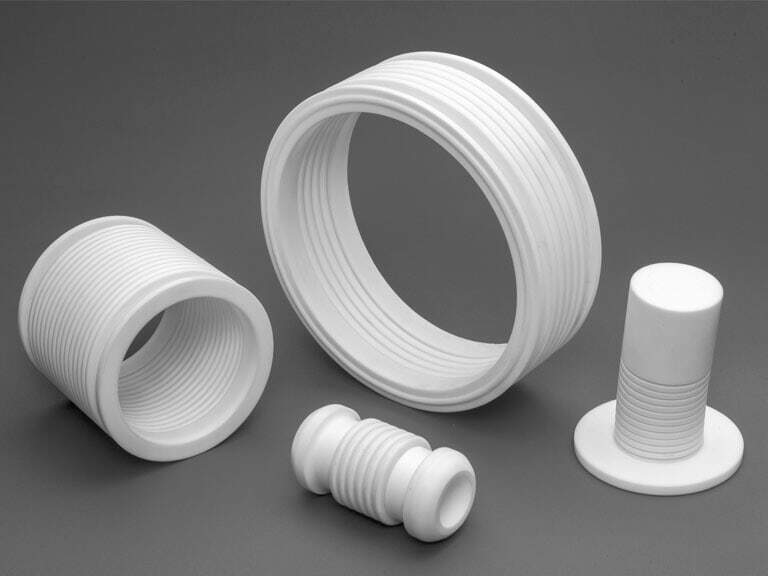
Table of Contents
ToggleWhat is PTFE?
Teflon is a common brand name for the thermoplastic fluoropolymer polytetrafluoroethylene (PTFE). PTFE is chemical resistant and stable even at high temperatures, and despite its mediocre mechanical properties, it is one of the popular CNC machining and milling plastics for many specific applications. PTFE takes the form of a white solid at room temperature and is generally notably resistant to chemicals such as bases and acids. Additionally, designers in the medical, cookware, and automotive industries often use PTFE because of its low coefficient of friction properties.
Advantages of Teflon
Most of PTFE’s properties derive from its nature as a thermoplastic fluoropolymer, which contains only carbon and fluorine. Notable properties of Teflon include:
- Fatigue and chemical resistance
- Anti-ultraviolet, waterproof
- High insulation performance
- Low coefficient of friction
- Melting point 327°C
- CNC Machining PTFE parts are anti-stick
- Thermal stability between -260°C and +260°C
Limitations of PTFE
Although PTFE is a very popular engineering plastic with advantages for a variety of applications, CNC machining of PTFE still has certain limitations. These include:
- The cost is relatively higher.
- Low mechanical strength.
- Its tensile strength is lower than that of nylon.
- PTFE parts react with alkali metals and fluorinating agents.
- PTFE produces toxic fumes when exposed to temperatures above 500°F (260°C).
Mechanical properties of PTFE:
- – Density: 2.15 g/cm3
- – Surface hardness: SD63
- – Tensile strength: 1,500 – 3,000 PSI (25 MPa)
- – Flexural Modulus: 72,000 PSI (0.70 GPa)
- – Water absorption (soaked for 24 hours): <0.01%
- – Coefficient of friction (dynamic): 0.10
Common grades of PTFE
Manufacturers in different industries use different grades of PTFE when CNC machining PTFE parts. Some of these PTFEs have brand names and unique properties. The following are common CNC-machined Teflon grades:
- Pure PTFE has high chemical resistance, bending performance and electrical performance;
- Peek filled PTFE – for better compressive strength.
- Pigmented PTFE – for better visibility.
- Pure PTFE – High chemical resistance, electrical and flex properties.
- Chemically modified PTFE – less creep, improved permeation resistance, smooth surface.
- Glass-Filled PTFE - Ideal for producing parts requiring excellent chemical resistance, abrasion resistance and high compressive strength.
Ideal Technology for Manufacturing Teflon Parts--CNC Machining
You’ll be hard-pressed to find Teflon parts made by injection molding or 3D printing. CNC machining is the most commonly used method of manufacturing Teflon parts. It is a subtractive process that utilizes computer-controlled tools to remove portions of Teflon material to create the desired part.
Greater precision and fewer defects
CNC machines offer greater precision when manufacturing Teflon parts because they require little human intervention. CNC machining of PTFE parts is likely to be less error prone. CNC machines maintain repeatability and this error rate, the risk of defects during CNC machining of PTFE is low.
PTFE will decompose before high temperature
Teflon/PTFE exhibits high melt viscosity and sensitivity to heat in high temperature amorphous form. Therefore, CNC machining is ideal for processing PTFE, as it may deteriorate before it is melted.
Also, processing Teflon/PTFE at temperatures above 250°C produces some toxic gases. These gases can have a physically detrimental effect on both the mechanic and the end product user. Injection molding and 3D printing are not suitable for making Teflon parts due to the high temperatures required.
CNC machining is suitable for parts with complex shapes
3-axis, 4-axis, 5-axis CNC machines provide the precision and accuracy required for complex Teflon/PTFE parts. This vital quality makes CNC machining an integral part of precision Teflon machining.
Multi-axis machines use tools that can move in 4 or more directions, allowing Teflon parts to be machined from different angles at the same time for better results.
PTFE is very sensitive to heat
Most manufacturing methods, including CNC machining, generate heat during the manufacturing process due to the movement and interaction of the tool with the workpiece. Therefore, you should employ an effective cooling system to manage the heat generated when CNC machining PTFE materials.
Teflon is very sensitive to heat. During Teflon processing, if there is no cooling system, defects such as warping may occur.
CNC Machining Process of PTFE Parts
CNC machining is a widely adopted technique for manufacturing a wide variety of custom Teflon/PTFE machined parts. Generally speaking, this subtractive process involves the use of computer-controlled tools to create Teflon material to create parts with specific shapes and dimensions. Rapid Fabricator uses different CNC machining processes to create custom Teflon parts. AN-Prototype summarizes the standard processing method of CNC processing Teflon:
1. CNC drilling
CNC drilling is the use of a drill to make holes in Teflon parts. It is important to note that it is critical to use tools that will assist in proper chip evacuation. Also, make sure the drill is perpendicular to the workpiece to mitigate drift.
2. CNC milling
CNC milling involves using a CNC milling machine to cut excess material from Teflon to create different parts. CNC milling machines rotate and move cutting tools along different axes. As a result, milling machines provide the high precision and accuracy required for a wide variety of PTFE machined parts. Therefore, CNC milling is suitable for making Teflon parts with rough edges.
3. CNC turning
The CNC turning process involves holding the Teflon material in a chuck, rotating the workpiece while feeding it into a turning tool to create a PTFE part with a hollow structure. CNC turning facilitates the manufacture of Teflon/PTFE parts in round or conical shapes with high precision.
4. CNC turning and milling compound machine
CNC mill-turn machining technology combines the characteristics of milling and turning methods to manufacture Teflon/PTFE parts with complex geometries. While CNC mill-turn machining may not be at the level of multi-axis machining, it can provide some complex parts, such as hollow Teflon parts with rough bottom characteristics.
5. Multi-axis/5-axis machining
5-axis CNC machining of Teflon is suitable for making complex custom parts. It utilizes multi-axis and multi-tool setups to manufacture PTFE parts. Most importantly, it ensures outstanding accuracy and precision in the final product. Tight tolerances are easier to achieve with 5-axis CNC machining processes.
Typical application of CNC machining Teflon/PTFE parts
CNC machined Teflon parts are widely used in various industries due to their excellent material properties. The following are typical applications for PTFE machined parts:
Aerospace industry
CNC machined Teflon parts exhibit excellent material properties such as good strength and low friction, making them suitable for use in the aerospace industry. PTFE is an excellent electrical insulator, making PTFE parts safe for electrical connections and cable insulation. Other uses of PTFE include fuel hoses, coatings and door surface protection.
Additionally, aerospace part designers use PTFE CNC machining because of its accuracy and precision in manufacturing aerospace parts with tight tolerances.
Medical industry
The medical industry often uses PTFE to make medical parts due to its chemical inertness and flexibility. PTFE machined parts are biocompatible due to their ability to maintain chemical and structural stability when used as body implants. A common example of a medical PTFE machined part is a valve.
Automobile industry
Typical applications of Teflon/PTFE in the automotive industry include valves and gears. In addition, PTFE is suitable for the manufacture of lightweight chassis and other vehicle components of various sizes and shapes.
Food processing industry
Teflon/PTFE is chemically inert, making it an ideal material in food processing. Therefore, Teflon processed parts will not react with processed foods. Typical applications for Teflon/PTFE CNC machined parts in this industry include food machinery components.
Alternatives to Teflon
While CNC machining PTFE has many advantages, other materials that are better alternatives include:
Ethylene Chlorotrifluoroethylene (ECTFE)
This is a copolymer of ethylene and chlorotrifluoroethylene, a semi-crystalline fluoropolymer. It is a fluoropolymer similar to Teflon, a fluorocarbon compound containing multiple carbon-fluorine bonds.
This semi-crystalline thermoplastic has better corrosion and chemical resistance than PTFE. Therefore, manufacturers often use it as parts that require better chemical and corrosion resistance.
Polychlorotrifluoroethylene (PCTFE)
This material is an alternative to Teflon, but is different because it is a thermoplastic chlorofluoropolymer. It has the lowest water vapor transmission rate of all plastics and a high water resistance rating.
Perfluoroalkoxy (PFA)
PFA and Teflon are both fluoropolymers with similar chemical resistance. But PFA is less abrasion resistant and is softer than Teflon. Therefore, manufacturers rarely use this material in structural parts.
Basic Precautions and Tips for CNC Machining PTFE
Teflon is a material that offers impressive flexibility when CNC machining. However, it is critical to understand certain factors that affect a Teflon/PTFE CNC machining project. Here are some of these factors:
Softness
Teflon is easy to CNC machine because it is a naturally soft thermoplastic. However, its extreme lack of rigidity can cause tool chatter during CNC machining. So, you can use a better grade of PTFE for your CNC machined parts, or introduce a material that increases its strength. Also, a general rule of thumb is to use a tolerance of +/- 0.001 per inch for plastic parts.
Tight tolerances
CNC machining PTFE to tight tolerances is difficult because Teflon/PTFE machining is susceptible to increased stress creep and high coefficient of expansion. However, closer to optimum tolerances and desired surface finishes can be achieved using water soluble coolants.
Extreme pressure deformation
Applying too much pressure when CNC machining PTFE will deform it.
sharp tool
Teflon is a versatile material that can be machined with a variety of tools including end mills. In particular, sharp tools work well when CNC machining thermoplastic polymers such as PTFE, nylon, and acrylic. This is because sharp tools produce clean cuts, which is critical when CNC machining Teflon as it is a non-stick material.
In addition, sharp knives help reduce friction between the tool and the material, reducing heat generation, which is also critical when CNC machining PTFE.
Coolant
The high heat generated during CNC milling or turning can cause PTFE to thermally expand, resulting in poor finishes and inaccurate tolerances. Use a teflon-compatible coolant and adjust coolant flow accordingly. The most commonly used coolants are compressed air, water-soluble coolants, and chemically inert sprays.
Deburring
Deburring is critical when CNC machining Teflon. The sharp edges created by the CNC machining process can cause problems during assembly and can also lead to premature failure of the part. Using a PTFE-compatible deburring tool or method, remove all burrs from the part.
Other PTFE CNC Machining Tips:
- Use the right machining tool for your Teflon machined part to ensure better chip clearance and avoid clogging.
- Carbide cutters with polished top surfaces are recommended for machining Teflon/PTFE parts for improved surface finish and tool protection.
- Sandblasting is an ideal surface preparation option for machinists to use to remove surface irregularities from CNC Teflon parts.
- Provide support for PTFE material during CNC machining to ensure high precision.
Although Teflon CNC machining is more challenging than other plastic parts, AN-Prototype can manufacture high-quality PTFE prototypes or small batches of PTFE parts. We are reliable CNC machining service specialists with years of experience in CNC machining Teflon/PTFE parts. We offer a wide range of machining capabilities including milling, turning and 5-axis CNC machining to produce high-quality, precise custom PTFE parts to tight tolerances.