According to incomplete statistics, there are 45 polymer series in the material library, up to 85000 kinds of plastics, which can be roughly divided into two categories: thermosetting plastics and thermoplastics. Injection molding is one of the most commonly used methods for manufacturing large quantities of parts. Choosing a suitable material seems to be a difficult task. This requires us to have a detailed understanding of materials, and must refer to the purpose, efficiency and cost of manufacturing parts. Of course, some materials may be more suitable, but there is no “one size fits all” situation for injection molding process. Selecting the right material can improve the shape, assembly and function of the part. In the final analysis, the selected material is always directly related to the application of the part.
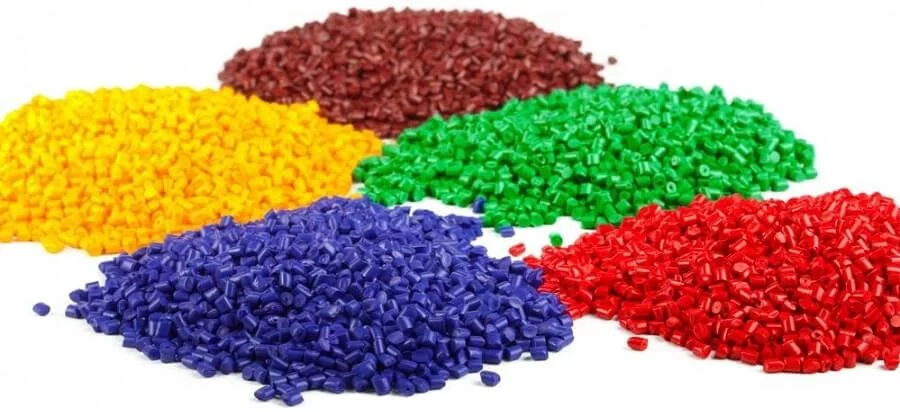
Table of Contents
Toggle1.The difference between thermosetting plastics and thermoplastics.
The main difference between thermosetting plastics and thermoplastics lies in their different reactions to heat, resulting in distinct outcomes.
a. Thermosetting plastics
This material increases in strength when heated or exposed to high temperatures; for example, thermosetting plastic products can maintain their overall strength and shape even in environments with exposure to high temperatures. This characteristic is beneficial in manufacturing large permanent parts and components as they can withstand more usage and extreme conditions. However, thermosetting plastics also have obvious drawbacks as their internal structure changes when heated, making it impossible to reshape or reuse them. The high melting point of thermosetting plastics is also not suitable for injection molding processes, and not all thermosetting plastics have the same melting point. Each material reacts differently to heat, so specialized machines may be required for a particular type of thermosetting plastic, and they generally cannot be used interchangeably.
b. Thermoplastic
Thermoplastic materials do not undergo a chemical change in their structure after multiple heating and cooling cycles, making them recyclable materials that can be reused. In terms of injection molding, thermoplastic materials have a relatively low melting point, which is a significant advantage and makes them more suitable for large-scale manufacturing of plastic parts. However, thermoplastic materials generally have a higher cost than thermosetting plastics.
2.Factors to consider when selecting materials
Reverse thinking may be helpful in finding the right material for your plastic parts. Prepare to answer these questions: What will the parts be used for? What kind of pressure will they endure? Will they be working in harsh environments? Is the assembly complex? Prioritizing these factors can help in selecting the appropriate material.
a. Installation position
The installation location of the component is a factor that must be considered, whether it will be placed in sunlight, outdoors, humid environments, or installed inside a larger assembly.
b. temperature
Will the component be operating in a cold refrigerator, at room temperature, or in high-temperature environments such as under the hood of a car?
c. life cycle
The average working time of parts is 5 years, 10 years, or more?
d. Guarantee
Specific to the automotive industry, it is necessary to consider the possibility of component failure several years down the line. What will be the cost of repair?
e. Cost limitation
Commodity-grade plastics such as high-density polyethylene or polypropylene are typically high in density and relatively inexpensive. Another type is engineering plastics, such as PEEK, PEI, and other materials, which are highly resistant to high temperatures and very durable, but have a higher cost.
f. Appearance requirements
Does the component require texture, how high does the surface finish need to be, and would colored parts be more suitable than transparent ones, among other considerations.
Once you have answered the initial questions, you can eliminate the majority of materials, but you still need to consider a series of follow-up questions to further narrow down the range of materials.
g. Design function
Consider the mechanical properties of the part, whether it needs to be flexible, compressible, or bondable, etc. Does it need to have tensile strength? What are the requirements for the part’s impact resistance, electrical insulation, etc.? Does the material need to bond with components, such as multi-material overmolding or insert molding? The weight of the part is also an important consideration factor.
h. Environmental factor
What will be the working environment for the part? Will it come into contact with chemicals? Does it need to be flame retardant? What are the requirements for UV resistance?
i. Complies
For certain industries, there are specific material requirements for parts. Does your part need to be food grade certified, comply with FDA standards, or meet medical grade, ISO, electrical compliance, or other standards?
3.Advantages and applications of commonly used thermoplastic materials
A professional injection molding factory usually offers dozens of stock engineering-grade plastics and must also support more special materials as requested by customers. According to the inventory of materials provided by a Chinese injection molding supplier, DDPROTOTYPE, the advantages and applications of commonly used thermoplastic materials are summarized.
a. ABS
I. Advantage
ABS is a tough and impact-resistant plastic that has low shrinkage and stable dimensional properties, as well as excellent acid and alkali resistance, and is widely used in different fields. This material is relatively inexpensive in price.
II. application area
Including but not limited to electronic products, remote controls, computers, telephones, cosmetics, handheld devices, and casings.
III. Note
Injection molded parts made from ABS will show knit lines and may have sink marks and voids in thicker areas. Fortunately, ABS can be blended with PC to greatly improve the material and solve these issues.
b. ABS/PC
I. Advantage
ABS/PC blend material combines the strength and heat resistance of polycarbonate with the flexibility and dimensional stability of ABS, making it a material with excellent mechanical properties. This material has higher heat resistance than ABS and higher impact resistance than PC in low temperature conditions.
II. application area
These blend materials are commonly used in the automotive, electronics and telecommunications industries, as well as other industries.
III. Note
ABS/PC material maximizes the solution to defects in single-material molding, such as thick molding issues. This blend material can be chosen when excellent mechanical performance is desired while also aiming to reduce costs.
c. PC
I. Advantage
PC is a transparent plastic with high optical transparency, high strength, extreme impact resistance, low shrinkage, and good dimensional stability. Additionally, PC has excellent heat resistance and parts processed from it have a high surface finish.
II. application area
Including but not limited to lenses, lighting fixtures, mobile phone cases, electronic components, medical devices, and bulletproof glass.
III. Note
When manufacturing thicker parts from PC, voids, bubbles or sink marks may occur. Additionally, PC parts have relatively poor chemical resistance. ABS/PC blend material is a good substitute for PC and can address some of these defects, but the resulting parts are opaque.
d. PA or PPA
I. Advantage
PA, or polyamide, is a high-performance engineering plastic with outstanding mechanical properties, excellent corrosion resistance, oil resistance, and heat resistance. By reinforcing and flame-retardant modification, its heat resistance, stability, and flame retardancy can be significantly improved. There are many types of nylon (4, 6/6, 6, 6/10, 6/12, 12, etc.). Each material has its own advantages. Nylon has high strength and high temperature strength, as well as excellent chemical resistance. For example, nylon 6/6 has high strength and hardness, and is very wear-resistant. At low temperatures, nylon 6 is very hard and tough. Nylon 6/12 has better impact resistance.
II. application area
Not limited to parts with thin wall features, shafts, gears and bearings, screws, pumps, guides, etc.
III. Note
Nylon is prone to deformation, which is common knowledge. In some specific environments, such as inside a humid refrigerator, it is generally advisable to avoid choosing nylon parts. This is because nylon is a hygroscopic material, which can cause changes in the dimensions and structure of the parts and result in damage.
e. POM
I. Advantage
It is tough, rigid, hard, and strong, and is among the hardest of plastics. It also has good lubricity and resistance to organic solvents, and excellent elasticity. Therefore, this plastic is very suitable for manufacturing bearing surfaces and gears.
II. application area
Including but not limited to gears, pumps, impellers, blades, conveyor chains, fans, switch components, buttons and knobs.
III. Note
Due to its shrinkage, uniform wall thickness is necessary when manufacturing parts from POM. Its lubricity makes it difficult to paint or coat, and achieving an aesthetically pleasing finish can be challenging.
f. PMMA
I. Advantage
Also known as acrylic, it is another transparent plastic with good optical properties, surface smoothness, scratch resistance, and low shrinkage.
II. application area
Not limited to lenses, light tubes, optical lenses, lampshades, optical fibers, logos, etc.
III. Note
PMMA is relatively brittle and prone to cracking under stress, and it has poor chemical resistance.
g. PP
I. Advantage
PP has good moldability, good surface stiffness and scratch resistance, and is a relatively low-cost plastic. It has good impact resistance, wear resistance, high toughness, good elongation, and acid and alkali resistance.
II. application area
Including but not limited to hinges, fans, bottle caps, medical transfer pipettes, etc.
III. Note
PP tends to become brittle in low temperatures. The production of thicker parts may result in the formation of bubbles, shrinkage, or warping.
h. PBT
I. Advantage
PBT is an excellent engineering material with good toughness and fatigue resistance, high heat and weather resistance, good electrical properties, and low water absorption. Reinforcing and flame-retardant modification can significantly improve its heat resistance, dimensional stability, and flame-retardant properties, making it ideal for automobiles and providing excellent electrical performance for electronic components. It has moderate to high strength and toughness, and good resistance to fuels, oils, fats, and many solvents, and does not absorb odors.
II. application area
Including but not limited to sliding bearings, gears, grinders, vacuum cleaners, buttons, etc.
III. Note
PBT resin is prone to warping and it is difficult to process into thin-walled parts.
i. PPSU
I. Advantage
PPSU has the characteristics of high toughness and heat resistance, and is a material that is resistant to high temperatures and dimensionally stable. It also has the ability to resist radiation and a certain degree of acid and alkali resistance.
II. application area
Including but not limited to medical device components, sterilization trays, hot water fittings, sockets, and connectors.
III. Note
For thicker parts, PPSU may result in gaps or bubbles. Organic solvents and hydrocarbons have some corrosive effects on PPSU materials. Colorants generally cannot be added to PPSU resin.
j. PEEK
I. Advantage
PEEK is a high-temperature resistant, chemically resistant, flame-retardant, and dimensionally stable material commonly used in the medical, aerospace, and automotive industries.
II. application area
Including but not limited to bearings, piston components and pumps, insulated wires, etc.
III. Note
PEEK is a high-performance material, so the cost is very high.
The 11 materials mentioned above are commonly used materials for injection molding. DDPROTOTYPE also offers other plastic options, such as PPS, TPE, TPU, LCP, HDPE, LDPE, and PSU, which can be further enhanced by adding glass and carbon fibers to improve their performance.
4.Typical materials for medical injection molding.
For a long time, people have believed that plastics have more advantages than metals in medical applications because metals may undergo chemical reactions with the saltwater solution in the human body. In the injection molding process, the medical industry has the highest requirements and a huge demand. The quality of medical injection molded parts is related to people’s health and may even endanger their lives. When working with medical injection molding manufacturers, it is important that they fully understand the characteristics of the most commonly used thermoplastic plastics in medical injection molding, and this is also one of the performance indicators of whether the manufacturer complies with strict manufacturing standards. Below, we will introduce the commonly used materials and their applications for medical injection molding parts. Typically, these medical materials are not used as backup stock materials but need to undergo strict testing before being used in production.
a. PE
Polyethylene (PE) is the most widely used plastic in the world so far. It is a cost-effective medical-grade material that is non-absorbent, non-biodegradable, and does not fade, making it an ideal choice for sensitive medical equipment and components. Polyethylene is resistant to retaining dangerous bacteria and can withstand harsh cleaning agents. It is commonly used for containers, bottles, and pipes, but is susceptible to UV radiation and is flammable. Its tensile strength is 4,000 psi.
b. PP
Polypropylene is a thermoplastic material with excellent mechanical properties and chemical resistance. It is strong and durable, with a very high tensile strength of 4,800 psi, and is used in a range of applications from automotive bumpers to medical tools. Polypropylene is commonly used to manufacture disposable syringes, connectors, finger joint prostheses, non-absorbable sutures, containers, medicine bottles, and transparent bags.
c. PS
Polystyrene is one of the most widely used plastics. It is a glassy and transparent plastic that is relatively inexpensive, but has poor barriers to oxygen and water vapor, and a relatively low melting point. Polystyrene is commonly used to manufacture test tubes, culture dishes, trays, and disposable plastic utensils.
d. PMMA
PMMA has nearly perfect visible light transmittance and an unusual characteristic of reflecting light beams inside its surface, making it commonly used for manufacturing optical fibers. It is also used in medical devices to produce artificial teeth, dental implants, denture materials, dental fillings, artificial lenses, and membranes used for dialysis.
e. PVC
Polyvinyl chloride (PVC) is one of the most commonly used thermoplastic polymers in the world. It is primarily used in the construction industry, such as for flooring, pipes, and wall panels in hospital sterile laboratories. In some cases, it is used as a substitute for rubber, and is also commonly used to manufacture materials for blood dialysis or perfusion, blood tubing, blood bags, and prosthetic limbs.
f. PC
Polycarbonate is a group of thermoplastic polymers with natural transparency to visible light and UV resistance, often used in eyeglass lenses and considered a good substitute for glass. Polycarbonate is a very strong material that is not easily broken and is also commonly used in medical devices. Parts made with polycarbonate can be sterilized using steam at 120°C, gamma radiation, or ethylene oxide (ETO) methods.
5.Looking for a trusted injection molding manufacturer.
When entrusting your injection molding project to a manufacturer, you expect them to consistently meet your expectations and add value to your project. Therefore, you need to know what to look for in an injection molding manufacturer.
a. Proper injection molding certification.
The injection molding industry has strict guidelines, especially for special industries such as medical.
b. Design and fabrication certification.
It is very important that the manufacturer’s equipment meets the quality standards of IQ/OQ/PQ process validation. In addition, the use of design software such as Solid Works CAD is an important indicator of their prototyping capabilities.
c. Quality control and evaluation certification.
For manufacturers, ISO 9001:2015 is an important certification as it signifies an appropriate quality management system.
d. Material safety and procurement certification.
A. The quality control level of the manufacturer.
Injection molding requires high stability, and it is essential that your supplier maintains quality control and safety measures throughout the entire production process. Visiting their factory to see if they have the capability to manufacture a range of thermoplastic plastic parts is crucial. It’s also wise to ask them to describe specific case studies of their practices.
B. Internal manufacturing equipment and professional mechanics.
Internal advanced manufacturing equipment and skilled machinists are essential foundations for providing high-quality and meeting production expectations. A 5-axis CNC machine, a coordinate measuring machine, and other equipment are necessary conditions. Of course, experienced machinists need to track the entire development process. If you have any questions when choosing injection molding materials, please do not hesitate to contact AN-Prototype. They will provide advice for you based on over 20 years of experience, free of charge.