Complex surfaces are widely used in various industries, such as the automotive industry and the aerospace industry. Due to the rapid improvement of science and technology, in the face of more complex surface accuracy and complex part shapes, the quality requirements are more stringent, which requires more innovation and improvement in the current CNC machining technology in order to ensure the quality of the produced curved surface parts. The precision and quality correspond to the requirements of production. Among them, in the process of implementing CNC machining, the accuracy of complex curved surface parts will be affected by the error problem, so it is necessary to strictly control the CNC machining error, and apply corresponding means to reduce the error of complex curved surface parts, so that the machining accuracy can be reduced. Efficiency is improved.
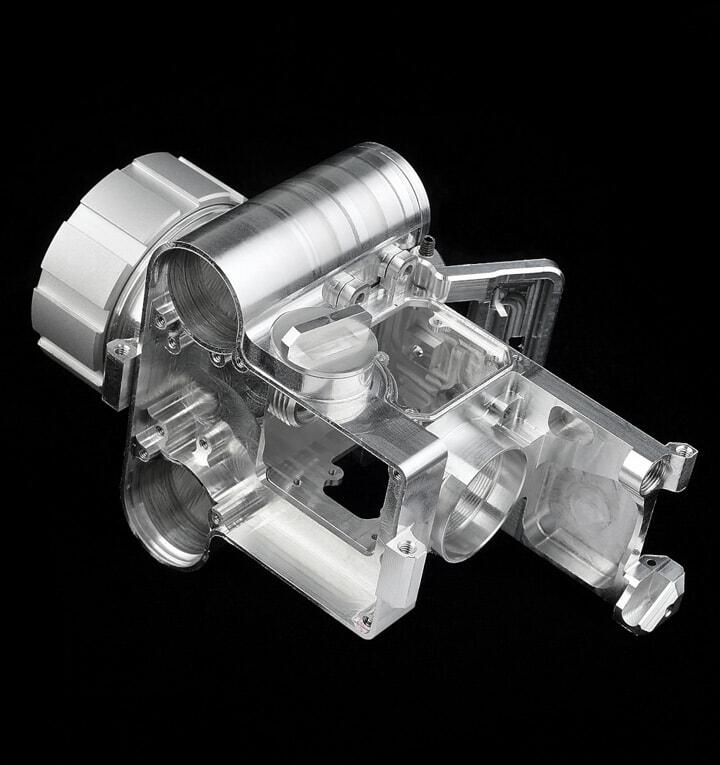
Table of Contents
Toggle1. The status quo of complex and comprehensive CNC machining
Usually, the application of CNC machining technology is a very precise processing method for complex curved surface processing, but there are some factors that affect its processing accuracy, resulting in errors. For example: applied prop materials, surface models and processing methods, etc. In the process of specific operation, there will be a certain error between the application theoretical running track of the tool and the interpolation track. If it is not strictly controlled, it will produce greater machining errors and reduce work efficiency. At present, the high technology of five-coordinate linkage CNC machining and three-coordinate CNC machining technology are widely used. Although they play a very important role, there are also some unavoidable influencing factors. At present, in CNC machining, the main tools used include spherical cutters, end mills, and ring cutters, because any point in the spherical cutter will have the same effect after contacting the curved surface, because most of the spherical cutters are used on the curved surface. It is very suitable for three-axis simultaneous CNC machining and five-axis simultaneous CNC machining, but only ring tools are suitable for five-axis simultaneous machining. Although CNC machine tools are very precise, there are still many influencing factors. Therefore, controlling and analyzing their errors is a key link to improve processing efficiency.
2. Error analysis of complex surface CNC machining
The main factors that cause errors in CNC machining of complex surfaces are the geometric errors of the machining tools, the geometric motion errors between the machining surfaces and the machining tools, and the manufacturing errors generated by the process system. Generally, the NC machining errors of complex surfaces include: tool axis The error caused by the swing, the error caused by the linear approximation. In the specific machining process, the part with the most errors is around the center of the interpolation break, which is composed of the maximum rotation error and the maximum linear approximation error. The rotation error is the error generated when the normal vector rotates. Specifically, it is the error generated by the normal vector during the rotation process. The factors that affect the size of the transmission error are the radius processing compensation of the tool and the arc length of the curved surface. , The normal curvature of the processed surface. The linear approximation error will be affected somewhat by CNC machining complex surface shapes, but the machining tool will not have a great impact. In short, the radius of the tool, the line of the tool, the step size, and the specific shape of the geometry of the machined surface will cause corresponding errors in the machining. In NC machining of complex curved surfaces, the interpolation chord length will have a direct impact on the linear approximation error. If the linear approximation error needs to be reduced, it is necessary to reasonably control the feed rate and interpolation cycle of the tool.
3. Error control of complex surface CNC machining
(1) Tool axis rotation error compensation
In the CNC specific machining of complex curved surfaces, if the machined surface is a convex curve along the direction of the cutting tool, then the running track of the cutting point is a concave curve. In such a case, the machining error will be relatively large, and the sum of the tool axis rotation error and the linear approximation error will also be relatively large. If the method of cutting the contact point of the tool is used, the rotation error of the tool shaft can be compensated to a certain extent, so that the total error can be reduced. Moving the cutting point A of the tool along the normal vector direction of the processing surface to A’ becomes a new cutting point, which can change the distribution of NC machining errors on complex curved surfaces and make the machining errors compensated[ 3]. If the surface in NC machining of complex curved surfaces is a concave curve along the tool-feeding direction, and the linear approximation difference 1 exceeds the tool axis rotation error n, there will be no over-tolerance. Therefore, there is no need to implement machining error compensation, and the tool axis rotation error compensation should be controlled in a reasonable way in combination with the specific situation.
(2) Straight line approximation error control
In the NC machining of complex curved surfaces, a straight line will approach the curved surface. For this situation, there will be a straight line approximation error 1. Specifically, the interpolation operation will cause a straight line approximation error 1. Generally, In this situation, the linear approximation error can only be reduced or effectively controlled, but it cannot be completely eliminated. Effective ways to control the linear approach error include controlling the interpolation chord length, interpolation period control and controlling the feed rate of the tool.
One, interpolation chord length control. In the process of CNC machining, if there is no change in the machining surface, the normal curvature of the feed direction in the interpolation break is a fixed value. At this time, the interpolation chord length is the factor that affects the linear approximation error, and the linear approximation error and The square of the interpolation chord length is proportional, so reducing the interpolation chord length can reduce the linear approximation error in CNC machining to some extent. If ≥ 1 , then. Therefore, in the NC machining of complex curved surfaces, the interpolation chord length needs to be strictly controlled so that it is within the corresponding range, so as to guarantee the machining accuracy. Therefore, shortening the interpolation chord length reasonably is an effective measure to reduce the linear approximation error, which can improve the accuracy of CNC machining. But it should be noted that it cannot be shortened infinitely. In machining, the interpolation chord length period of CNC coefficient and the feed speed of the tool play a decisive role in the interpolation chord length [4]. Secondly, the interpolation cycle and feed speed, in the specific machining of curved surface, the feed speed and interpolation cycle of the CNC system will have a direct impact on the interpolation chord length, usually, the NC technology can set the interpolation cycle The staff determines the feed speed. In the case of no change in feed rate, the shorter the interpolation cycle, the smaller the interpolation chord length. Therefore, the linear approximation error is also smaller. Similar to it, in the case of no change in interpolation, a smaller feed rate will produce a smaller interpolation chord length, so the linear approximation error will be smaller. For the application of NC system with a small interpolation period, in the process of NC machining, the feed speed of the tool should be reduced as much as possible, so that the error of NC machining of complex curved surfaces can be reduced.
In short, in the CNC machining of complex curved surfaces, some errors will inevitably occur. It is important to use reasonable methods and measures to control these errors in order to make the errors smaller and ensure the quality of CNC machining.