PEEK (polyether ether ketone) is an advanced engineering plastic with several beneficial properties. These include high temperature elasticity, abrasion resistance, biocompatibility, ultra-high vacuum resistance, excellent chemical resistance, and suitability for CNC machining. PEEK is a semi-crystalline thermoplastic that can operate continuously at temperatures up to 260°C and is highly chemical resistant. It must be noted, however, that certain acids such as sulfuric acid will dissolve the material. CNC machining PEEK is a common method for manufacturing parts used in extreme environments that require mechanical strength, chemical stability and/or high temperature resistance. Applications include components for the medical, aerospace and automotive industries.
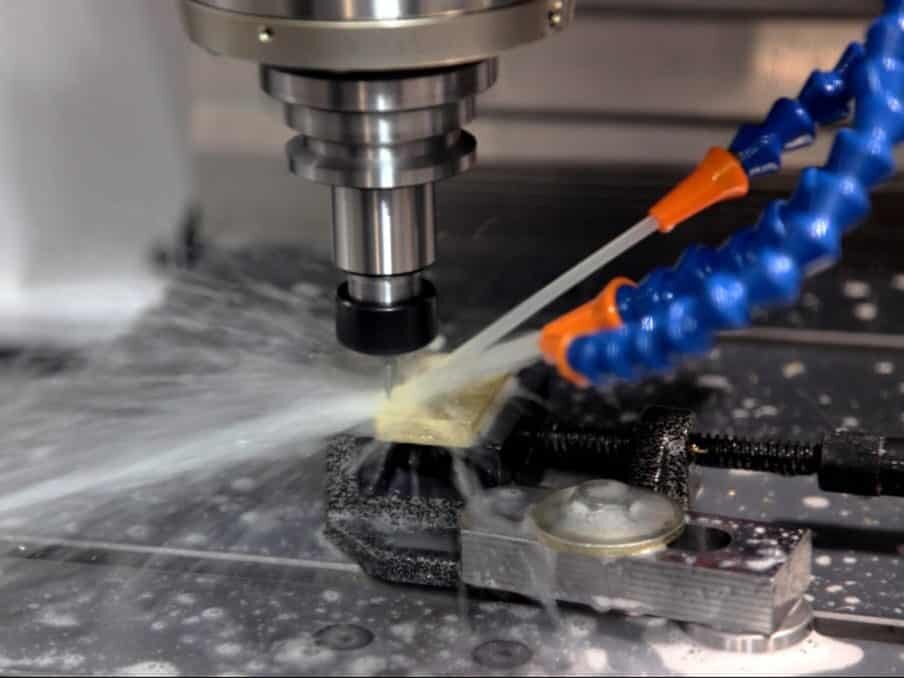
Table of Contents
ToggleWhat is polyetheretherketone (PEEK)?
First discovered in 1978, PEEK is incredibly resistant to heat, abrasion and fatigue. PEEK is also resistant to creep, meaning it retains its shape in harsh environments and high temperatures, as well as under mechanical stress. PEEK is not only tough, but also lightweight and easy to manufacture. Because PEEK is physically lightweight yet highly resistant to corrosive substances, it is ideal for many manufacturing methods. PEEK can be processed using injection molding or additive manufacturing to make custom parts, and its high melting point (343°C) allows for faster feeds and speeds. PEEK can also be CNC machined to make parts. Among various manufacturing methods, CNC machining PEEK is repeatable and accurate, and can produce parts with tight tolerances.
There are two types of common PEEK: industrial grade PEEK, medical grade PEEK and glass fiber reinforced PEEK.
Industrial grade PEEK
Industrial grade PEEK is a strong, flame retardant, abrasion resistant thermoplastic with high impact strength and low coefficient of friction. It is known for maintaining its mechanical properties even at high temperatures. As the name suggests, this grade is most commonly used in the aerospace, automotive, chemical, electronics, petroleum, and food and beverage industries.
- Tensile strength: 14,000 psi
- Tensile modulus: 590,000 psi
- Water absorption: 0.50% over 24 hours
- Melting point: of 343°C (nearly 650°F)
- UL 94 V-0 flammability rating: (0.059″ thickness)
Medical grade PEEK (TECAPEEK)
PEEK compliant with USP Class VI standards, such as TECAPEEK MT, are biocompatible variants specifically designed for use in medical technology. It is characterized by very high chemical resistance, resistance to various sterilization methods and the ability to maintain its mechanical properties at high temperatures. Medical grade PEEK is typically used in medical applications and devices that require limited contact with skin and tissue. USP Class VI PEEK withstands multiple sterilization cycles without degradation.
- Tensile Strength, Yield (MPa) :96.5-110
- Elongation at Break (%):30-50
- Hardness (Rockwell M):94-99
- Heat Deflection Temperature (°C):160
- Glass Transition Temperature (°C):150
Glass Fiber Reinforced PEEK - PEEK GF30
GF30 PEEK is a 30% glass filled variant of PEEK. GF30 offers superior rigidity and higher mechanical strength compared to general purpose unfilled PEEK. Glass-reinforced PEEK also offers greater dimensional stability and creep strength. This material is ideal for parts subject to high static loads at elevated temperatures. Due to the abrasive effect of glass fibers on mating surfaces, PEEK GF30 is less suitable for bearing or abrasive applications.
- Tensile Strength, Yield (MPa):101-157
- Elongation at Break (%):2.2-5
- Hardness (Rockwell M):103
- Heat Deflection Temperature (°C):316
- Maximum Service Temperature (°C):260-300
Characteristics of PEEK
1. Excellent chemical resistance, electrical resistance and temperature resistance
PEEK material has high chemical resistance. It has similar corrosion resistance to nickel steel and maintains a non-corroding and intact chemical structure even at high temperatures. Under normal circumstances, only concentrated sulfuric acid can dissolve this plastic.
PEEK has high electrical performance at high temperature and high frequency. Due to its stable chemical structure when subjected to chemical attack, PEEK parts can perform flawlessly under high doses of ionizing radiation.
PEEK also has high resistance to gamma radiation, more significantly than polystyrene (the most radiation-resistant material in general-purpose resin applications). This characteristic makes it suitable for high-performance wires to ensure good insulation.
PEEK material is very durable and has a high melting point. Therefore, it works very well during high temperature peak processing and does not deform at higher temperatures.
2. High processing rate, stable performance even at high temperature
PEEK material ensures high machinability during plastic CNC machining due to its good processing properties. Although it is an ultra-high temperature thermoplastic material, it can be processed with different material processing methods.
These methods include injection molding, extrusion molding, melt spinning, and the like. The high temperature processability and high thermal decomposition properties of PEEK ensure this compatibility. Additionally, this thermoplastic is a self-extinguishing material during combustion; it produces little or no toxic gases and fumes.
3. Excellent mechanical properties, creep resistance, wear resistance, friction resistance.
PEEK and other high temperature thermoplastics have high impact strength and retain their dimensions at elevated temperatures. It has a low coefficient of linear expansion and good dimensional stability. PEEK has the highest fatigue and stress retention properties of all other plastics. In addition, it has excellent creep resistance (the ability of a substance to deform slowly under prolonged stress). This characteristic makes it a suitable material to withstand enormous stresses during processing. PEEK has excellent wear resistance and a low coefficient of friction. Therefore, it maintains high wear resistance under various physical pressure conditions, surface roughness, temperature and speed relative to the contact surface.
4. Low water absorption, radiation resistance
Using PEEK to make machine or instrument parts helps those parts maintain their chemical structure and performance in wet areas. Its resistance to hydrolysis even at elevated temperatures makes it ideal for wet environments, pressurized hot water or steam.
Factors to be considered in CNC machining PEEK parts
PEEK is a very adaptable material, but there are some engineering considerations to keep in mind to ensure the best results.
#1 Annealing PEEK Plastic Before CNC Machining
Annealing: Since PEEK has lower elongation than other plastics, it may crack if drilled deeply. Special handling is often required to minimize thermal cracking and other internal stress damage. This requires annealing the PEEK plastic prior to processing. PEEK plastic is typically available in various sizes as rods, sheets or injection molded blanks. But before you can start machining these parts, the accumulated stress must be removed by annealing. This is a heat treatment process that involves heating the plastic to a predetermined temperature, holding it for a certain period of time, and then cooling it to room temperature.
Annealing increases the crystallinity of PEEK parts and reduces internal stresses, preventing the possibility of surface cracks during CNC cutting operations. One thing to note though: If you plan to machine PEEK workpieces for extended periods of time, you may need to perform an additional annealing process.
#2 Using Carbide and Polycrystalline Tooling
All PEEK grades are abrasive to cutting tools ㅡ meaning they can cause damage, wear to the tool during CNC cutting operations. Therefore, we recommend that you use carbide tools for small batches of common PEEK grades. However, for glass fiber and carbon fiber reinforced PEEK grades, you may want to consider polycrystalline (PCD) tooling, especially for long manufacturing runs.
#3 Use the Right Coolant
For example, although PEEK is very heat-resistant, it does not dissipate heat well and must be cooled during CNC machining to prevent breakage or deformation. Standard liquid coolant (petroleum based) is ideal when cutting industrial grade PEEK plastic. But standard liquid coolants can affect the biocompatibility of medical-grade PEEK, making it unsuitable for making medical components. At AN-Prototype, we recommend that you cool medical grade PEEK plastic with compressed air or purified water.
#4 Use correct CNC machining parameters
To CNC machine PEEK parts without surprises, you need to ensure that you are using the correct machining parameters when performing drilling, milling, and turning operations. AN-Prototype summarizes the ideal cutting speed and feed rate ranges for manufacturing PEEK parts.
#5 Avoid Pollution
Contamination is a serious concern when processing medical-grade PEEK plastic because it can affect its biocompatibility. Therefore, protective gloves should be used when handling PEEK parts. Additionally, you should keep processed medical-grade PEEK parts in airtight containers to prevent contamination.
Applications of PEEK Parts
The three main industries that use PEEK components are the industrial sector, the healthcare sector, and the food and beverage industry.
Industrial application
Industrial grade PEEK is essentially pure and has high mechanical and chemical stability. This minimizes contamination and maximizes safety for chemical and energy applications as well as components for the automotive, aerospace and electronics industries. In industrial wheels and pumps, PEEK even outperforms metals such as stainless steel.
Medical Application
PEEK can make components for the healthcare industry, such as orthopedic devices and spinal fusion devices. When manufactured using biocompatible methods, PEEK can also be used in dental implants, prosthetics, and more.
Food and Beverage Applications
PEEK was recently approved by the U.S. Food and Drug Administration (FDA) as safe for human contact when properly prepared. Now, PEEK is making its way into the food and beverage industry for components such as cookware, beverage dispensers and nozzles, and processing applications.