CNC machining motorcycle parts requires skill, knowledge, and attention to detail, but the results can be truly impressive. By understanding the basics of CNC machining, the materials used in motorcycle parts, advanced techniques, design considerations, and tips for success, you can achieve great results in your work. Whether you are designing parts for a client or working on your own project, CNC machining can help you create high-quality, durable, and efficient motorcycle parts that will stand the test of time.
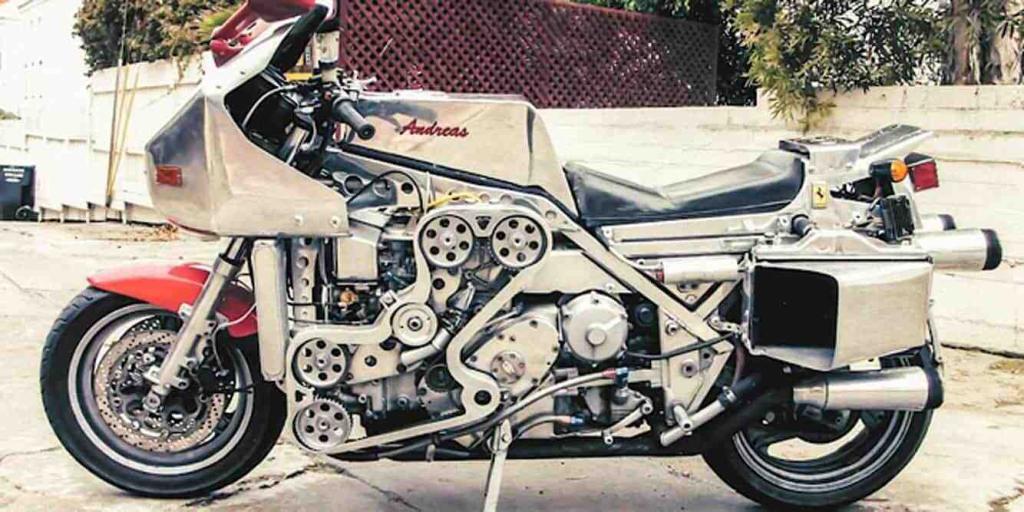
Table of Contents
ToggleBenefit Of CNC Machining Motorcycle Parts
It’s no secret that designing and crafting motorcycle parts is a time-consuming process. From conceptualizing the design to the finalizing stages of production, it can take several weeks or even months to develop high-quality and functional pieces. However, with cutting-edge technology like CNC machining, designers can speed up the process and enhance their capabilities by producing unique and immaculate motorcycle parts that offer an array of benefits.
1. Precision: The precision resulting from CNC machining can’t be compared to any other production process. With its ability to create intricate designs, CNC machining can create even the smallest and intricate motorcycle parts with high proficiency. This precision and accuracy in design make for flawless fit-ups, improving the overall quality of the finished product.
2. Lower production cost: It’s no secret that conventional manufacturing strategies can be expensive. However, CNC machined parts can lessen production costs as the detailed technical drawings used in the process minimize the action involved for each part. This reduces the amount of material waste, full use of raw materials and thus reducing costs. Less waste equals less material cost, allowing for more cost-effective mass production of the required parts.
3. Improved efficiency: When it comes to motorcycle parts, precision is crucial. Using CNC machining, designers can increase their production capacity and improve production speed. By using high-speed tools and fast turnaround times, designers can produce high quality and unique parts with utmost efficiency for their customers.
4. Superior quality: The quality of parts produced by CNC machining is higher compared to conventional manufacturing processes as CNC machining can produce intricate and complex designs. Lean manufacturing processes guarantee that each item produced is of consistent, high quality.
5. Flexibility: One of the significant advantages of CNC machining is the quick, easy, and painless changeover from one part to another. This efficiency ensures that designers can switch from creating one piece to another without significant downtime. Furthermore, with the multiple axis ability, CNC can attain exceptional accuracy in angled motorcycle parts without a secondary operation.
Common CNC Machining Motorcycle Parts
Motorcycle enthusiasts prefer customizing their rides to make them stand out in a crowd. There are several parts and accessories that can be customized according to an individual’s preference. CNC machining is a popular method used for manufacturing custom motorcycle parts. From CNC machined sprockets to handlebars, there are various aspects of a bike that can be upgraded using this method.
1. CNC Machining Engine Casings
CNC machining technology has revolutionized the manufacturing process of motorbike engine casings. The benefits of CNC machining are vast, including the efficient use of raw materials, higher precision and accuracy, freedom of design, and lower costs. The flexibility of the technology enables the production of complex and intricate designs, allowing the creation of custom engine casings to meet the needs of each client. With CNC machining, the production process of engine casings has become streamlined, efficient, and cost-effective, resulting in higher quality and higher performing motorbikes.
2. CNC Machined Triple Trees
CNC machined triple trees are necessary for the stability and handling of a motorcycle. They connect the front forks to the frame and hold the steering stem. CNC machining offers precise dimensions, accurate angles, and tight tolerances to ensure a perfect fit. Riders can choose from different designs to suit their style.
3. CNC Machined Footpegs
Footpegs are essential for a comfortable ride. CNC machined footpegs offer superior grip, durability, and an improved aesthetic. Riders can choose from a range of materials like aluminum, titanium, or stainless steel. Some footpegs come with adjustable height to match the rider’s comfort level.
4. CNC Machined Handlebars
Handlebars are another essential part of the motorcycle that can be customized using CNC machining. Riders can choose from different designs and materials, including aluminum, carbon fiber, and titanium. CNC machining allows for precise dimensions, thickness, and shape to meet individual preferences.
5. CNC Machined Sprockets
CNC machined sprockets are a popular modification of the bike’s rear wheel drive. They can be customized according to the desired shape, size, and number of teeth. CNC machining offers greater accuracy and precision in the manufacturing process, which results in a better and smoother ride.
6. CNC Machined Brake Calipers
Brake calipers are necessary for ensuring the safety of the rider. CNC machining provides a higher degree of precision, which is necessary for the proper functioning of the brakes. CNC machined brake calipers offer greater durability, better heat dissipation, and enhanced performance.
7.CNC Machining Motorcycle Wheels
The motorcycle industry has benefited immensely from CNC machining, especially in the manufacturing of wheels. CNC machining provides precision, speed, and cost-effectiveness that traditional manufacturing techniques cannot match. When designing motorcycle wheels using CNC machining, it’s essential to follow best practices to ensure that the final product is of the highest quality. Whether you’re a seasoned CNC parts designer or a beginner, using CNC machining for motorcycle wheel manufacturing will undoubtedly take your expertise to the next level.
Materials Suitable For CNC Machining Motorcycle Parts
Choosing the right material is crucial for producing high-quality motorcycle parts using CNC machining. Aluminum alloys are popular due to their lightweight and high strength-to-weight ratio, steel alloys for their strength, titanium alloys for their high-performance properties, copper alloys for their electrical properties, and plastics for their low cost and ease of machining. It’s essential to consult with machining professionals to determine the best material for your motorcycle part application.
Aluminum alloys:
Aluminum alloys are a popular choice for motorcycle parts due to their lightweight and high strength-to-weight ratio. They are also corrosion-resistant and easy to machine. CNC machining aluminum parts is a popular choice for motorcycle engine components like cylinder heads, rocker arms, and valve retainers. Some of the popular aluminum alloys suitable for CNC machining include 6061, 7075, and 2024.
Steel alloys:
Steel alloys are suitable for CNC machining but are heavier than aluminum, making them ideal for structural components. The most common types of steel used include carbon steel, stainless steel, and tool steel. Carbon steel is the most widely used steel for motorcycle parts due to its high tensile strength, weldability, and low cost. Stainless steel is preferred where corrosion resistance is required, while tool steel is for parts that require high hardness and wear resistance.
Titanium alloys:
Titanium alloys are a popular choice for producing high-performance motorcycle parts. They have high tensile strength, corrosion resistance, and are biocompatible, making them perfect for screws, bolts, and fasteners. However, they are difficult to machine and require specific tooling and cutting parameters. Some of the popular titanium alloys used in motorcycle parts include Grade 5 and Grade 9.
Copper alloys:
Copper alloys are popular for producing electrical components, but they are also suitable for producing motorcycle parts due to their high thermal conductivity, corrosion resistance, and low friction coefficient. Some of the popular copper alloys used in motorcycle parts include brass, copper-nickel, and bronze. They are ideal for producing bushings, washers, and gears.
Plastics:
Plastics are also suitable for CNC machining, and some of the commonly used types include polycarbonate, ABS, and nylon. They are lightweight, durable, and corrosion-resistant, making them perfect for body panels, fairings, and seats. Additionally, they are easy to machine, and their low cost makes them an excellent choice for low volume production.
CNC Machining Processes for Motorcycle Parts
There are various machining processes used in industries to fabricate various motorcycle parts. CNC turning and milling appear to be the basics. Although, there are other methods like drilling. Let’s take a detailed look into some of these machining processes.
CNC Milling
CNC milling refers to the use of computer numerical control to produce complex parts with high precision. CNC milling machines use a computer-controlled cutter to remove materials from a workpiece according to specifications. CNC milling is highly popular in the customization of motorcycle parts, allowing designers to create parts that are tailored to specific motorcycle models.
CNC Turning
CNC turning has a high precision level. The machines can produce components to within a few microns. This makes it ideal for the production of complex motorcycle parts. With CNC turning, designers can produce intricate parts with high accuracy, which is essential for tension structures, shafts, and gearboxes that require precision machining.
Precision Grinding
Precision grinding is a critical process in designing motorcycle parts that need to meet high-performance standards while also ensuring safety. Using CNC machining in the precision grinding process allows designers to achieve the desired level of accuracy, consistency, durability, and cost-effectiveness. By paying attention to the materials used and overcoming some of the challenges in the process, CNC can help in creating finer quality and complex parts as needed by any motorcycle enthusiast.
CNC Drilling
CNC drilling is a powerful tool for creating precise, durable, and custom motorcycle parts, but it also requires careful attention to detail and collaboration between designers, engineers, and manufacturers. By following best practices and tips for success, designers can leverage CNC drilling to produce parts that are both functional and aesthetically pleasing, while satisfying the needs and preferences of motorcycle riders. Whether you're a veteran CNC parts designer or just starting out, mastering CNC drilling for motorcycle parts is a crucial skill that will help you stay ahead of the competition and deliver value to your clients.
Laser Cutting
Creating motorcycle parts with precision and accuracy can be challenging and time-consuming. Laser cutting is one process that caters to the production of motorcycle parts with intricate and complicated designs. The numerous advantages of laser cutting, including precision, durability, speed, versatility, and cost-effectiveness, make it a suitable technique for designing motorcycle parts. As a CNC parts designer, incorporating laser cutting for motorcycle parts production could benefit your design process through its efficiency, accuracy, and quality.
EDM Machining
EDM machining can be an efficient process for machining motorcycle parts. This is because it is a non-contact process that removes material through erosion. Compared to traditional CNC machining, which requires a cutting tool to remove the material, EDM machining has no physical contact with the workpiece, making it less prone to wear and tear. This feature makes EDM machining a highly repeatable process that can produce accurate parts with improved efficiency, thereby reducing the chance of errors and ensuring high-quality parts.
Motorcycle Parts Surface Finishes
Surface finish of motorcycle parts is essential to the aesthetics, performance, and durability of the parts. As a CNC parts designer, it’s crucial to choose the right surface finish that meets the unique needs of your customers. Whether you choose polished, anodized, powder coating, or chrome finish, each option has its benefits and drawbacks. By understanding the different surface finishes, you can make an informed decision and improve the quality of your motorcycle parts.
Polished Finish
The polished finish is one of the most popular surface finishes for motorcycle parts. This finish gives the parts a mirror-like appearance and smooth texture, enhancing their visual appeal. However, polished finishes are not just for aesthetics; they also provide corrosion resistance and easy maintenance. Polishing removes any impurities, scratches, or burrs from the surface, leaving a clean and smooth surface.
Anodized Finish
Anodizing is an electrochemical process that creates an oxide layer on the surface of aluminum parts. This process improves the mechanical and chemical properties of the materials, making them more resistant to wear, corrosion, and heat. Anodized parts also have a decorative finish that adds to their value and appeal. The color of the anodized finish can range from natural gray to vibrant colors, depending on the dye used in the anodizing process.
Powder Coating Finish
Powder coating is a dry finishing process that involves applying a powder coating on the surface of the motorcycle parts. The powder is electrostatically charged, enabling it to adhere to the surface and form a vibrant and durable coating. The powder coating offers several benefits, such as corrosion resistance, UV stability, and color versatility. Powder coating is also an eco-friendly process, as it produces less waste and VOC emissions than other coating methods.
Chrome Finish
Chrome plating is a surface finishing process that involves electroplating a thin layer of chromium on the surface of motorcycle parts. Chrome plating improves the aesthetics of the parts, giving them a shiny and reflective finish. Chrome parts also provide corrosion resistance, increased hardness, and wear resistance. However, chrome plating can add weight to the parts, making them less suitable for high-performance motorcycles.
Tips For Custom CNC Machining Motorcycle Parts
Custom CNC machined motorcycle parts are becoming more popular. It’s because they can add personality to bikes. While some bikers’ love for buying aftermarket parts, others prefer creating their unique motorcycle part.
1. Choose The Right Material
The material you choose for custom CNC machined parts determines the finished product’s quality. Some popular materials to choose from include titanium, aluminum, copper, brass, magnesium, and steel. Before selecting your material, consider the part’s usage, the environment, and the budget.
2. Consider The Part’s Functionality
When creating custom CNC machined motorcycle parts, it’s essential to consider the part’s purpose. Ask yourself questions like, what will it do, how it will fit, and whether the material and design are optimal for the role it’s intended to perform.
3. Use Appropriate Cutting Tools
CNC machining involves more than simply programming a machine. The cutting tools you use can make or break the final product’s quality. Customized tools achieve the perfect fit and design for a specific part. Additionally, reusing old cutting tools and investing in lower-quality cutters will affect the final product.
4. Pay Close Attention to the Design
A well-thought-out design conveys a sense of professionalism. When designing a custom motorcycle part, it’s essential to pay attention to details. The design must be suitable for the material you’re using.
5. Prototype Before Production
Creating prototypes provides a visual understanding of what works and what needs improvement before starting production. Prototyping cuts lead times while assuring the final product’s quality. Additionally, it helps identify design flaws, integration issues, and potential highs and lows in production costs.
Trustworthy CNC Machining Motorcycle Parts Manufacturer
AN-Prototype‘s commitment to sustainable and advanced production technology means that they use cutting-edge CNC machines to manufacture their motorcycle parts. Their CNC machines can manipulate various materials, from metals and plastics to ceramics. With this, they provide a wide range of customization options for their clients. AN-Prototype’s professionals use their expertise to ensure customer satisfaction by producing finished motorcycle parts to the highest quality standards. They guarantee their customers complete satisfaction by offering personalized services with attention to detail, precision, and fast delivery.
Expert finishing is paramount in creating customized motorcycle parts; AN-Prototype understands this. The company uses nitriding, plating, and anodizing techniques amongst many others to guarantee the strength and durability of the motorcycle parts they produce. Their finishing techniques also ensure a high-quality, eye-catching look. AN-Prototype’s skilled artisans often customize motorcycle parts to meet their client’s individual and specific requirements.
AN-Prototype has a wide network of loyal customers, owing to their professional and personalized CNC Machining services for motorcycle parts. They guarantee that each part they create will meet customer satisfaction. AN-Prototype’s clients are assured that they will get the ultimate ride because they understand that authenticity, functionality, and aesthetics are what matter most to motorcycle enthusiasts.
AN-Prototype is passionate about providing its customers with high-quality motorcycle parts. They believe in giving their clients complete transparency on material used, part quality, and delivery time. AN-Prototype’s professionals can create custom motorcycle parts for all types of bikes, regardless of their brands. A combination of their technology, experience, and expertise means that AN-Prototype will significantly improve a motorcycle’s performance and appearance – customization, in fact, comes to life with AN-Prototype’s CNC Machining services.
Customizing a motorcycle is like building your dream machine. At AN-Prototype, they understand this and possess the necessary skills, equipment, and passion to ensure that your dream motorcycle becomes a reality. If you are a CNC parts designer or a motorcycle enthusiast looking to customize your ride, then AN-Prototype’s CNC Machining services are the perfect solutions for you. The company’s cutting-edge expertise in the industry has earned its place as a frontrunner in CNC Machining services in China for motorcycle parts. Partner with AN-Prototype today to breathe life into your vision and create a truly unique and personalized ride that you will be proud of.