CNC machining is fast becoming the leading method for manufacturing medical parts. The medical industry requires precise and high-quality components. CNC machining makes it possible to create these parts with a high degree of accuracy, consistency, and speed. However, this technology is sophisticated, and understanding how it works is essential. The technology is versatile enough to work with a wide range of materials, making it suitable for all types of medical parts. The process requires strict adherence to best practices and guidelines to meet the specialized requirements of the medical industry. With CNC machining, the medical industry can ensure high-quality patient care and better outcomes for patients.
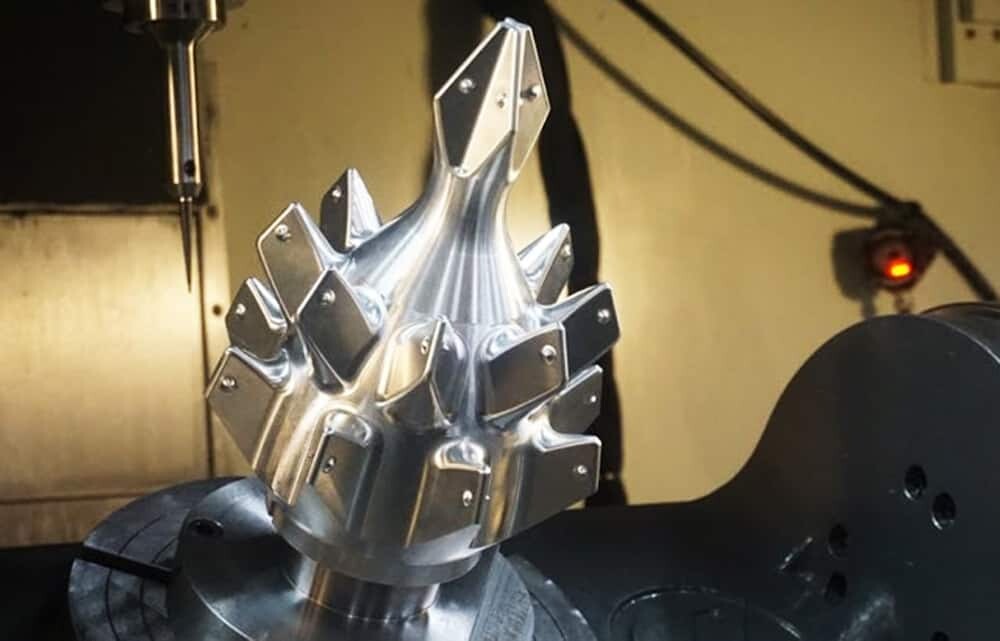
Table of Contents
ToggleWhy Medical Parts Need CNC Machining
The medical industry is one of the most complex and regulated industries in the world, and there is no room for errors in the manufacturing process. As a result, manufacturers of medical devices are required to meet strict quality standards while also ensuring that their products are ergonomic, functional, and aesthetically pleasing. In this context, computerized numerical control (CNC) machining has emerged as a crucial technology for medical device manufacturers. This technology allows for the production of complex, highly precise parts with minimal variation in manufacturing.
1. High Precision
CNC machining allows for the production of parts with tolerances that are impossible with manual machining techniques. CNC machines can achieve tolerances of as low as 0.0002 inches, making them ideal for the manufacturing of medical devices that require high precision. In addition, CNC machining allows for the production of complex parts with repeatable accuracy, reducing the chances of errors in large-scale manufacturing. Parts produced using CNC machines are also consistent in terms of their shape, size, and quality, ensuring that the medical devices function as intended.
2. Versatility and Flexibility
CNC machining is versatile and can be used to manufacture parts from a variety of materials, including stainless steel, aluminum, brass, and plastics. This technology can also produce parts of various shapes and sizes, making it suitable for the production of intricate medical devices such as surgical tools, implants, prosthetics, and medical equipment. What’s more, CNC machines can be reprogrammed quickly, allowing for rapid prototyping and design iteration.
3. Efficiency and Cost-Effectiveness
CNC machining is an automated process, which means that once a machine is set up, it can work for extended periods without interruptions, leading to increased efficiency. CNC machines can also produce parts with minimal waste, reducing the cost of materials. Moreover, the automated process eliminates the need for labor-intensive operations such as manual milling, drilling, and turning, reducing labor costs.
4. Quality Control and Traceability
As mentioned earlier, the medical industry is highly regulated, and manufacturers must adhere to strict quality standards. CNC machining has made it possible to automate many of the quality control functions, such as inspection and testing of the parts. This automation ensures that the parts meet the required specifications, reducing the chances of defects and eliminating the risk of human error. Additionally, CNC machining provides traceability, which is essential in the medical industry. Each part produced has a unique serial number, making it easier to track and trace the parts when needed.
5. Innovation and Customization
CNC machining technology is rapidly evolving, and this has allowed medical device manufacturers to push the boundaries of what is possible. This innovation has led to the development of new materials and designs, which have resulted in more effective and efficient medical devices. Furthermore, CNC machining allows for customizations and personalizations of medical devices, making them more patient-specific. This level of customization has resulted in a better patient experience and outcomes.
Materials Used In CNC Machining Medical Parts
It is evident that various materials are used in medical instrument machining to meet the array of surgical equipment requirements. Effective medical machining requires high attention to detail, which is why it is critical to choose the right material for each application. As a mechanical designer, it is important to keep these materials in mind when designing new medical instruments. Ultimately, ensuring that medical instruments are made using the appropriate materials will help to increase patient safety and the success of medical procedures.
Aluminum
Aluminum alloys, such as 6061 and 7075, are frequently used in medical instrument machining applications due to their unique characteristics. The 6061-series aluminum alloys are commonly used for applications that require formability, weldability, machinability and corrosion resistance. This series of aluminum is best suited for parts that will undergo bending, forming and punching processes. Additionally, 6061 alloys are a common choice for orthopedic implants and medical devices due to their excellent corrosion resistance and biocompatibility.
In contrast, the 7075 series of aluminum alloys are most commonly used in applications that require high strength and rigidity, such as surgical instruments and implants. 7075 aluminum is excellent for components that need to withstand high stress levels, and is ideal for use in applications that require natural anodized and hard-coated surfaces.
Another aluminum series used in medical instrument machining is the 2024 series. This series is best suited for parts that require high strength-to-weight ratio, making it a popular choice for medical devices and instruments. Medical instruments made with 2024 series aluminum can handle impact and sudden changes in temperature and humidity, which is necessary in various medical environments, including surgical rooms and laboratories.
The 5000 series of aluminum alloys are used in various biomedical applications for their unique blend of strength, high corrosion resistance, and medium to high strength properties. 5000 series aluminum is widely used in surgical instruments and implantable devices, having low density and a good strength-to-weight ratio. Due to the high fatigue, and fracture resistance, this alloy series meets regulatory requirements making it a preferred choice in consumer and medical applications.
Stainless steel is the most common medical instrument material because it is highly corrosion-resistant, easy to machine, and has a relatively low cost. It is also non-magnetic, making it an ideal material for MRI instruments. Its toughness can also be increased through heat treatment, making it an exceptional preference for surgical instruments.For instance, 316L stainless steel is used in orthopedic implants due to its high corrosion resistance and biocompatibility. Meanwhile, 17-4 PH stainless steel is used in dental implant screws due to its high strength and stress resistance.
Titanium
Titanium is another popular metal used in medical CNC machining. It has a high strength-to-weight ratio, excellent corrosion resistance. Pure titanium is radiopaque, making it easy to visualize in medical imaging.Titanium is commonly used in medical instrument machining due to its lightweight, biocompatibility, and corrosion resistance. Orthopedic implants like plates, rods, and screws are frequently made of premium grade titanium. Moreover, titanium is flexible, making it ideal for medical tools like forceps and clamps.
Cobalt-Chromium Alloy
Cobalt-chromium alloy features high mechanical strength, high ductility, and corrosion resistance. These notable features make it an excellent choice for dental implants, reconstructive implants, and cardiac implants. Its biocompatibility also makes it ideal for use in medical implants since it is less likely to cause an immune reaction.
Nitinol
Nitinol is a unique metal alloy made of nickel and titanium. It’s known for its shape memory and superelasticity properties, making it ideal for producing medical devices like stents. Nitinol stents can be compressed to a small size and inserted into a blood vessel, and then, they return to their original shape to prop open the blocked vessel. Nitinol is also biocompatible and corrosion-resistant, making it suitable for long-term implantation.
Polyetheretherketone (PEEK):
PEEK is a high-performance thermoplastic that is especially valuable as a material for medical instruments. This material is highly resistant to abrasion, chemicals, and high temperatures. Moreover, PEEK’s mechanical properties make it resistant to deformation, making it an ideal component in the creation of surgical instruments.
Polycarbonate (PC):
PC is a thermoplastic widely used in the production of medical instruments. It is a transparent and lightweight material that can withstand repeated sterilization processes and is also biocompatible, making it ideal for use in medical instruments such as blood filters and infant incubators.
Polypropylene (PP):
PP is a flexible, durable, and lightweight thermoplastic used in medical devices such as syringes and IV bags. The material’s ability to withstand a variety of sterilization techniques without the loss of its properties makes PP an excellent choice for medical instruments.
Acrylic:
Acrylic is a thermoplastic material ideal for medical instruments requiring transparency. This material can be used in surgical instruments like lenses and protective shields. It can also be molded into complex shapes and performs exceptionally well under UV radiation.
POM (Polyoxymethylene):
POM is a thermoplastic commonly used in medical instruments, including surgical tools and dental equipment. Its inherent strength and stiffness make it ideal for high-stress applications, and it performs excellently under high moisture conditions.
Applications Of CNC Machined Medical Parts
As the demand for precision medicine continues to grow, so too will the use of CNC machined parts. The application of these parts has revolutionized the medical industry and helped to improve the quality of healthcare around the world. The precision and accuracy that CNC machining provides make it an ideal tool for creating medical devices and implants. Moving forward, CNC machining will continue to play a vital role in the development and evolution of medical science.
1. Medical Implants:
CNC machined parts are used extensively in the manufacture of medical implants that are inserted into the human body. These implants need to be made with the utmost precision to avoid causing any damage to the patient. Titanium, as a material, is widely used in the production of medical implants due to its unique properties. CNC machining is the ideal method for producing these implants, as it allows for the creation of parts that are highly complex and accurate.
2. Prosthetics:
As the demand for prosthetic limbs and body parts continues to grow, CNC machining has become an essential tool in their manufacture. Medical practitioners can produce exact replicas of body parts most especially if they had experience in hyperrealism replicas. By using CAD/CAM (Computer-Aided Design/Computer-Aided Manufacturing) techniques, CNC machines can automate the process of fabrication and can create complex parts that meet the specific requirements and shapes that are needed for the prosthetic device.
3. Surgical Tools:
CNC machined parts are also used in the surgical tools that medical professionals use during operations. These tools need to be made from materials that are resistant to corrosion and are easy to sterilize. CNC machining, combined with advanced materials like stainless steel and titanium, ensures that surgical tools are durable and can withstand the rigors of frequent use. They can also be designed with precision and accuracy that ensures the physician’s control over the tool is optimized.
4. Dental & Orthopedic Devices:
CNC machining has had a major impact on the production of dental and orthopedic devices, as these devices require high precision in their manufacture. Dental devices such as braces and aligners are produced using CNC machines, which ensures a perfect fit for the patient. Orthopedic devices such as knee and hip replacements are also produced using CNC machines, which ensures that they are made to exact specifications.
5. Drug Delivery Systems:
CNC machining is also used in drug delivery systems. Such drug delivery systems require an intricate design and must be produced to exacting tolerances. CNC machining comes in handy for manufacturing these devices, with the ability to reduce the margins of error and make the devices incredibly precise. For an example, insulin pens are made using CNC machining which allows for exact measurement in the device.
With The Right Manufacturer For CNC Machining Medical Parts
Medical equipment requires precise and accurate machined parts for it to be functional, reliable, and safe. As a mechanical designer, finding the right manufacturer to partner with for producing machined medical parts can be a daunting task. You need to evaluate your options, be mindful of quality, and ensure that your manufacturer is capable of meeting your specific requirements. In this blog post, we’ll share tips on how to partner with the right manufacturer for machined medical parts.
1. Look for manufacturers that are specialized in medical industry
The first step in selecting a manufacturer for machined medical parts is their specialization. Medical equipment requires outstanding precision, so it is highly recommended to work with a manufacturer that has a track record of producing parts for medical devices. Their understanding of the industry standards, regulations, and protocols will make them a valuable partner in achieving your goals.
2. Check for certifications and quality standards
Quality is a critical factor to consider when selecting a manufacturer for machined medical parts. Make sure to check if the manufacturer has any certifications such as ISO 13485:2016, which is an international quality management system for medical devices. Other quality standards may include compliance to FDA regulations and RoHS compliance. These certifications indicate that the manufacturer has taken the necessary steps to ensure reliable and consistent production of high-quality parts.
3. Look for manufacturers that offer comprehensive services
A manufacturer that can provide a wide range of services like precision machining, prototyping, mold making, and packaging is an advantage as it will reduce the time, effort, and money needed to partner with multiple vendors. It is always beneficial to have a single source for all stages of your project requirements.
4. Evaluate their communication and customer service
Clear communication and exceptional customer service are fundamental aspects of any partnership, especially when it comes to machined medical parts, where precision is critical. Partnering with a manufacturer that responds promptly, communicates effectively, and values your input will ensure that any potential issues are resolved efficiently, and your requirements are met on time.
5. Choose a manufacturer that embraces innovation and technology
With the advancements in technology, it is essential to partner with a manufacturer that has up-to-date software, modern equipment, and a willingness to embrace innovation. Improvements in technology can lead to cost savings, better product design, and enhanced efficiency.
Partnering with a manufacturer for machined medical parts requires careful considerations such as specialization, certifications, comprehensive services, communication, and expertise in technology and innovation. At the end of the day, your partnership should be based on a foundation of trust, reliability, quality, and exceptional customer service. Choosing the right manufacturer will give you the confidence you need to develop and deliver medical equipment that can improve and save lives.
AN-Prototype is your go-to company for medical CNC machining services. Our team of professionals is committed to ensuring the production of high-quality medical parts and prototypes that comply with industry standards. Whether you’re a start-up, an established business, or anywhere in between, we have the expertise to manufacture your medical products. Contact us today to learn more about our services, and let’s discuss your next medical device project.