CNC machining ABS is one of the great options for making parts. ABS material is currently the largest and most widely used thermoplastic engineering plastic. ABS organically unifies the various properties of PS, SAN and BS, and has excellent mechanical properties of toughness, hardness and rigidity. As a leading rapid manufacturer of CNC machining ABS parts for more than 15 years, AN-Prototype is equipped with 25 CNC machine tools, including 3 sets 5-axis, 15 sets 3-axis, 7 sets turn-milling machines. These CNC machines support our ability to manufacture prototypes, low-volume and high-volume production parts in ABS material.
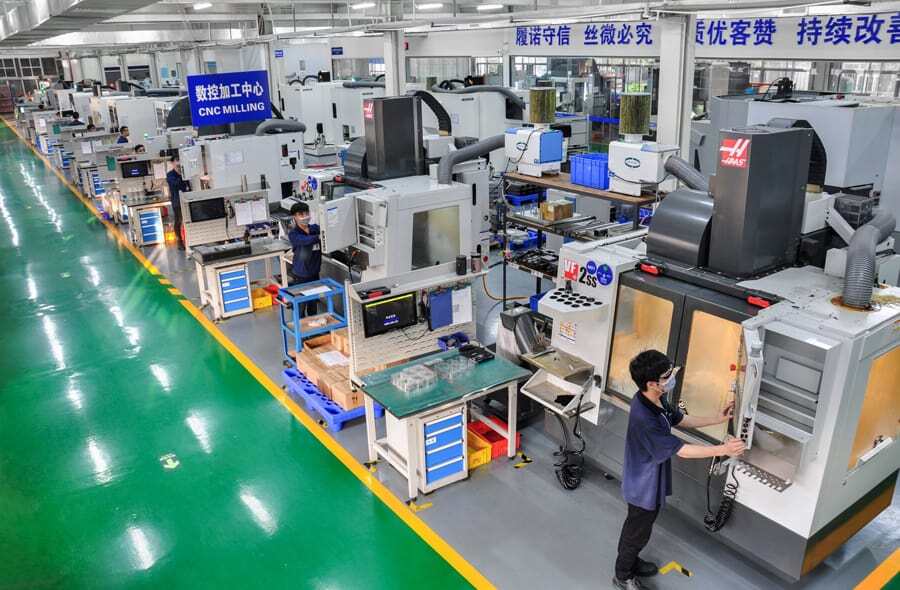
- Price: $ $
- Tolerances:0.05mm
- Wall Thickness:0.5mm
- Leading Time < 10 Days
- ISO 9001& ISO 13485 Certified
- 3 Axis, 4 Axis, 5Axis CNC Machining
- Max part size:2000 * 1300 * 600 mm
Table of Contents
ToggleCharacteristics of ABS plastic
ABS is a terpolymer composed of 15-35% acrylonitrile, 5-30% butadiene and 40-60% styrene. The acrylonitrile content gives the ABS its strength, the butadiene gives toughness, and the styrene gives a glossy, impermeable surface. Acrylonitrile butadiene styrene (ABS) is a low-cost engineering thermoplastic due to its good dimensional stability, excellent impact strength and ease of machining. ABS is often used for prototyping because it is easy to CNC machine and readily accepts paints and adhesives. ABS is also a popular material for 3D printing due to its relatively low melting temperature. ABS polymers are highly resistant to alcohols, alkalis, aqueous acids, concentrated hydrochloric acid, phosphoric acid and oils. These advantages make ABS an ideal choice for applications that require low-cost and wear-resistant parts such as enclosures and casings, and is widely used in a variety of industries: from automotive components to medical equipment, aerospace, to musical instruments and more.
Mechanical strength
ABS is a strong thermoplastic with a tensile strength of 29.6 – 48 MPa, so it can withstand high loads without warping or cracking. The internal structure of ABS is dense and full, with high mechanical strength and load-bearing capacity.
Impact Strength
ABS is able to withstand impact or high impact energy without loss of its properties and material failure in any form of material. ABS has an average impact resistance of 20 kJ/m² for notched sheets and 58 kJ/m² for unnotched sheets, making it a suitable material choice for applications where parts need to withstand periodic impacts, such as aircraft boarding. machine stairs.
chemical resistance
ABS plastic is resistant to most chemicals such as acids, alkalis, mineral and vegetable oils. But it can react with concentrated glacial acetic acid, aromatic esters and carbon tetrachloride.
Hardness
ABS plastic is known for its hardness (200 – 215 J/m). Rigidity and hardness make it resistant to scratches and abrasions. The hardness of ABS makes it useful for structural parts in different applications.
Electrical Insulation
High pressure shocks are not an issue with ABS parts. It works perfectly as an electrical insulation and resists the flow of electrical current, an essential quality in insulation applications.
Smooth Surface
A smooth surface is an aesthetic property that gives ABS parts an attractive appearance. The luster and sheen of the ABS surface make it useful in situations where aesthetic appeal is critical.
Flame Retardant
ABS can work at temperatures ranging from -50°C to 70°C without degrading any physical, mechanical or chemical properties. It exhibits excellent functionality in this temperature range. It is also known as an excellent flame-retardant plastic, which can slow down a fire by stopping it from spreading, or even stop it from spreading.
Cutter Tool Selection for CNC Machining ABS
The high machinability properties of ABS are suitable for all CNC machining processes including milling, turning, milling, drilling etc. CNC milling is the most common operation for ABS and is used to transform workpieces into parts of the desired shape. Milling with different tool sizes, from 1/8″ flat end mills to 1/64″ flat end mills, depending on specific requirements. Other operating parameters of CNC machine tools, such as feed speed, spindle speed, depth of cut, etc., need to be adjusted according to the tool size.
Of these, high carbon steel tools are best suited for ABS milling (and in some cases carbide tools). It is compatible with almost all feed rates and cutting speeds. Reducing cutting speeds and feed rates can cause heating and physical damage to ABS workpieces. High cutting speeds (spindle speeds) may cause chipping.
For example:
Tool Dimensions (1/8″ flat nose end mill): Feed rate 1500 mm/min, 16,400 rpm, maximum pass length 1.27 mm.
Tool size (1/64″ flat end mill): Feed rate 762 mm/min, 16,400 rpm, maximum pass length 0.254 mm.
Source: (Emily A., 2019)
With larger tools, the RPM must be adjusted to a lower level, and it limits the maximum pass length. CNC machining of ABS and metal materials is very similar to machining of aluminum 6061. Clamping of ABS workpieces is mandatory and an optimal tool bar can be configured with the help of a CAM simulation.
Carbide tools are the best substitute for high carbon steel. It eliminates the possibility of fuzz on the top or bottom of the workpiece.
Precautions for CNC machining ABS
- Consider a minimum wall thickness of 0.5 mm to prevent warping.
- The depth of cut can be up to ten times the diameter of the tool head.
- The temperature of the tool needs to be monitored to prevent the tool from heating up rapidly.
- Coolants are required during drilling operations because hot chips can melt the material. Additionally, the material may stick as it exits the hole.
- Single-flute cutters are preferred until they clear chips well. In general, single-edged and double-edged tools are most common in ABS machining.
- Using carbide cutters limits frequent changing of cutter settings because of its longer life.
Application of CNC Machining ABS Parts
CNC machined ABS parts are widely used in automobiles, electronics, aerospace, home appliances, national defense, toys and other fields.
Automotive
Protective bumpers, steering and suspension parts, drivetrain spares, interior trim, wheel housings and more.
Medical Devices
Nebulizers, compressors, pharmaceutical packaging, ultrasound equipment, drug delivery, systems, laboratory equipment enclosures, etc.
Electronic Housings
Housings, insulators, computer keyboards, power plugs, power tool housings, etc.
Household Appliances
Refrigerator liner, vacuum cleaner parts, kitchen utensils, toys\refrigerator liner, juicer, etc.
Finishing Services for CNC machined ABS parts?
The surface treatment of CNC machined ABS parts presents a matte effect, which can be further processed to obtain the desired surface treatment effect. Some common finishing methods for CNC machining ABS parts include sandblasting, plating, and painting, among others.
Sandblasting – Sandblasting produces a smooth, matte texture with excellent visual appeal. ABS parts can be machined with abrasive grains such as sand, glass buds, steel, silicon carbide, etc.
Electroplating – Electroless plating and immersion plating enable the metallic coating of ABS surfaces. Common metals for ABS plating include aluminum, zinc, etc.
Painting – Binder painting is the most popular surface treatment method for CNC machining ABS parts. Any color can be painted on the surface as required. Additionally, painting of sandblasted ABS parts gives better results.
AN-Prototype's CNC Machining ABS Service
ABS is becoming more and more popular in CNC machining projects due to its low cost and excellent performance. Prototyping and mass producing precision ABS parts requires an in-depth knowledge of CNC machining technology and ABS properties.
An-Prototype is a professional service provider for ABS prototype and mass production. We have an experienced team of engineers and advanced CNC machines that can manufacture plastic and metal parts with very tight tolerances. If you’re looking for on-demand manufacturing services for your CNC machining projects, parts are just a few steps away. Send us your design and consult our engineers to complete it, then we will turn it into reality in no time.