All the finishing of a CNC machined part adds cost and manufacturing time to the part, but the right surface finish has the potential to bring your design vision to life. Surface treatments for CNC machined metal parts typically include various mechanical processes such as grinding, polishing and sandblasting, but chemical surface treatments such as passivation and anodizing are also available.
Chemical surface treatments can remove imperfections on metal parts and even change their electrical conductivity levels, prolonging their service life and also improving their wear and corrosion resistance. Chemical surface treatments have a range of industrial applications: in the aerospace industry, for example, chemical surface treatments are used to increase the durability of parts, increase thermal stability and slow down oxidation. In the electronics industry, chemical surface treatments can be found in the manufacture of everything from cell phone casings and game console casings to imaging equipment. While there are many chemical finishing options available, they are not necessarily suitable for every metal material. In fact, each chemical surface treatment is usually associated with a specific material and has its own advantages and disadvantages. In this guide, we’ll explore several common chemical finishing processes so you can decide which is best for your CNC project.
Table of Contents
ToggleFactors to Consider in Selecting Appropriate Chemical Surface Treatment
Passivation Stainless Steel
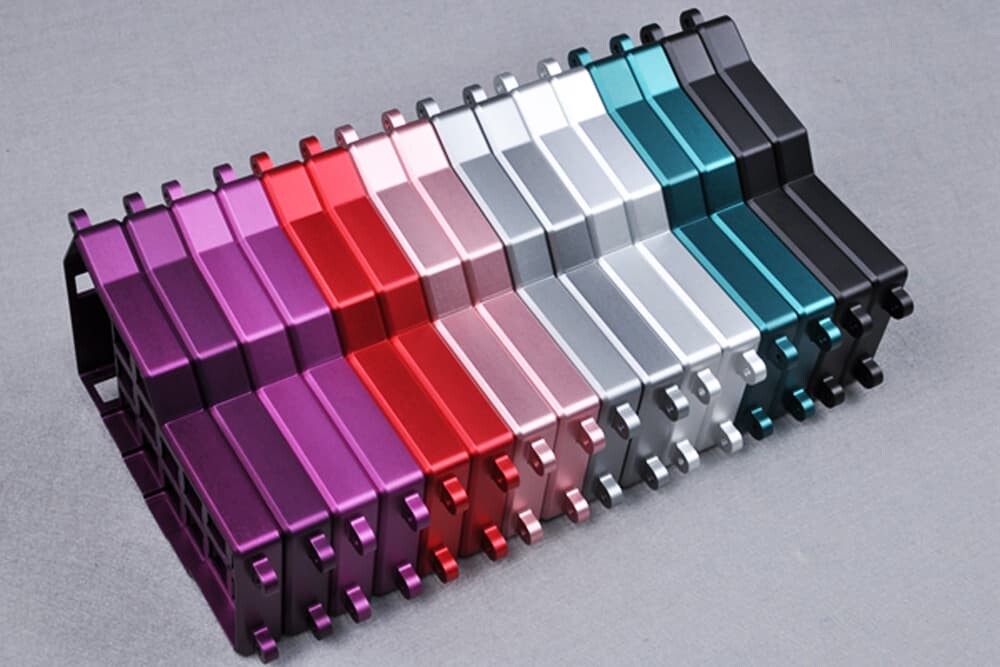
Anodizing Aluminum
When choosing the right chemical finish for your metal parts, you need to consider compatible materials and end use. This means considering a range of contextual factors, including:
- Environment where metal parts are used
- Whether conductive or insulating properties are required
- How much weight does the part need to support
- How much wear and tear the part needs to withstand
- Tolerance requirements for metal parts
- Color and Transparency Requirements
- Surface Finish Requirements
- Any other relevant or desired attributes.
To help you evaluate your options, AN-Prototype summarizes common chemical finishes and their compatible materials for your reference:
Anodizing: aluminum, titanium and other non-ferrous metals
Passivation: stainless steel
Black oxide: steel, stainless steel, copper and other metals
Chemical coating (chromate conversion coating): Aluminum
Electropolishing: Aluminum, Steel, Stainless Steel, Copper, Titanium, Brass, Bronze, Beryllium and its Electroplating Cadmium: Chromium, Copper, Gold, Nickel, Silver, Tin Aluminum, Steel and other metals
Chrome Plating: Aluminum, Steel, Stainless Steel, Nickel Alloys, Titanium, Copper and Other Metals
Polytetrafluoroethylene (Teflon™) Coating: Aluminum, Steel and Other Metals
Electroless Nickel: Aluminum, Steel and Stainless Steel
Galvanized: steel
Introduction to Chemical Surface Treatment
Let us learn about the process, how these chemical finishes work, and how they can benefit your CNC projects.
Anodizing
Anodizing is a popular finish option for aluminum and titanium parts that adds an oxide layer to the surface of the part, creating an anodic oxide film for added protection and improved aesthetics. For anodizing CNC aluminum parts, you dip the aluminum part into an acidic electrolyte bath, then use a cathode (the negatively charged electrode) to cause the solution to release hydrogen gas. At the same time, the CNC aluminum part (positively charged anode) releases oxygen, forming a protective oxide layer on its surface. After anodizing an aluminum part, its surface will have tiny pores that must be sealed with a chemical solution to prevent corrosion and the build-up of contaminants.
Anodized aluminum parts are durable and resistant to corrosion and wear, which can reduce maintenance costs. At the same time, the anodized layer is non-conductive and fully conforms to the aluminum substrate, so it will not chip or peel like plating and paint. In fact, in addition to sealing, the porous anodized layer can be painted or stained and is also more environmentally friendly since the anodized finish is non-toxic and chemically stable. Anodizing is not just for aluminum: the process is also suitable for titanium and other non-ferrous parts.
There are three different types of anodizing:
Type I (chromic acid anodizing) produces the thinnest oxide layer, which means it hardly changes the dimensions of the part. Type I anodized components will appear dull in color and will not absorb other colors well.
Type II (borosulfuric acid anodizing) has better oxide layer adhesion and is slightly thicker than Type I. With Type II anodizing you can easily create blue, red, gold, green, black anodized parts.
Type III (hard sulfuric acid anodizing) is the most common form of anodizing. It has the clearest finish, which means it works with more colours. It is worth noting that Type III anodizing results in a slightly thicker finish than Type II anodizing, which needs to be taken care of for parts requiring tight tolerances.
The increased durability, wear and corrosion resistance of anodized parts and the high level of dimensional control offered by the process have made anodizing particularly popular in aerospace, medical, automotive, electronics and more.
Despite its exceptional versatility, anodizing also has disadvantages:
Changing part dimensions: Anodizing metals changes the dimensions of the part, so the oxide layer needs to be considered when determining dimensional tolerances, or chemical or physical masking is used to ensure that specific areas of the part remain untreated, especially areas such as some holes.
Color matching is difficult. Achieving consistent color matching can be difficult if your anodized components are not processed in the same batch.
Not suitable for conductive applications. Anodizing metal parts increases their electrical and thermal resistance and is not suitable for conductive applications.
Passivation
Passivation prevents corrosion of stainless steel parts, helping them maintain cleanliness, performance and appearance. Not only are passivated parts more resistant to rust and therefore better for outdoor use, but they are also less likely to be pitted, last longer, look better and are more functional. As a result, passivation is used in a variety of industries, from the medical industry to aerospace with tight dimensional tolerances.
The passivation process involves the addition of nitric or citric acid. While nitric acid has traditionally been the typical choice for passivation, citric acid has recently grown in popularity because it reduces cycle times and is safer and more environmentally friendly. During passivation, stainless steel parts are immersed in an acid solution to remove rust from their surfaces without affecting the alloying element chromium in stainless steel. Applying acid to stainless steel removes any free iron or iron compounds from its surface, leaving behind a layer consisting of chromium (and sometimes nickel). After exposure to air, these materials react with oxygen to form a protective oxide layer.
It is important to remember that passivation can extend the manufacturing time of a part. Before passivating a part, it must be cleaned to remove any grease, dirt or other contamination, then rinsed and soaked (or sprayed). While immersion is the most common passivation method because it provides even coverage and can be done quickly, acid spray can also be used as an alternative.
Black Oxide Coating
Applied to ferrous metals such as steel, stainless steel and copper, the black oxide coating process involves immersing the part in an oxide bath to form a layer of magnetite (Fe 3 O 4 ), which provides slight corrosion resistance.
There are three types of black oxide coatings:
Hot Black Oxide: The hot black oxide coating process involves immersing the part in a hot bath of sodium hydroxide, nitrite, and nitrate to turn its surface into magnetite. After cleaning, parts need to be dipped in an alkaline cleaner, water and caustic soda, and then coated with oil or wax to achieve the desired aesthetic.
Medium Temperature Black Oxide: Medium temperature black oxide is very similar to thermal black oxide. The main difference is that coated parts will turn black at lower temperatures (90 – 120 °C). Since this temperature is below the boiling point of sodium and nitrate solutions, there is no need to worry about corrosive fumes.
Cool Black Oxide: Cool Black Oxide relies on deposited copper selenium to change the color of the part. Parts that receive a black oxide coating will have better corrosion and rust resistance, be less reflective, and have a longer life cycle. An oil or wax coating increases water resistance and also prevents harmful substances from reaching the inside of the metal, making the part easier to clean. The black oxide coating also adds thickness, making it ideal for drills, screwdrivers, and other tools that require a sharp edge that won’t dull over time. However, the wear resistance of cool black oxide is poor.
Chemical Film
A chemical film, also known as a chromate conversion coating, is a thin chemical coating typically applied to aluminum (although it can be applied to other metals as well) to prevent corrosion and improve adhesive and paint adhesion. Chemical film finishes often have proprietary formulations, but chromium is the main ingredient in each variety. Chemical film finishes can be applied by spraying, dipping or brushing and, depending on the product and formulation, can be yellow, tan, gold or clear in color.
While other finishes reduce thermal and electrical conductivity, chemical film finishes allow aluminum to retain its conductive properties. Chemical films are also relatively inexpensive and, as mentioned above, provide a good base for painting and priming (for the added bonus of time saving). However, chemical films are not ideal for aesthetically oriented CNC projects due to their susceptibility to scratches, scuffs, and other surface damage.
Electrolytic polishing
Electropolishing is an electrochemical finishing process commonly used to remove thin layers of material from steel, stainless steel, and similar alloys. During electropolishing, the part is immersed in a chemical bath and an electric current is applied to dissolve its surface layer. Various parameters affect the finish of the part, including the chemical composition of the electrolyte solution, temperature and exposure time of the part.
Electropolishing typically removes 0.0002 to 0.0003 inches from the surface of an object, leaving a smooth, shiny, and clean part surface. Other benefits of electropolishing include improved corrosion resistance, longer part life, improved fatigue strength, lower coefficient of friction, lower surface roughness, and elimination of surface defects such as burrs and microcracks.
Electropolishing is suitable for steel, stainless steel, copper, titanium, aluminum, brass, bronze, beryllium, etc. It’s worth noting that electropolishing is faster and less expensive than manual polishing, but it doesn’t 100% remove rough surface imperfections.
Plating
Electroplating is actually the reverse process of electropolishing. Instead of removing a layer of metal to achieve a final surface, electroplating deposits an additional layer that increases the thickness of the part. Compatible with cadmium, chromium, copper, gold, nickel, silver and tin, electroplating produces smooth parts that show less wear over time due to extra protection against corrosion, tarnish, impact and heat. Electroplating increases the adhesion between a substrate and its additional topcoat and, depending on the type of metal used, can make your part magnetic or conductive.
Compared with other CNC machined parts surface treatments, electroplating is not particularly environmentally friendly because it produces hazardous waste that can seriously pollute the environment if not handled properly. Plating is also relatively costly due to the metals and chemicals (and other necessary materials and equipment) required for plating, and can be time-consuming, especially when parts require multiple layers.
Chrome Plating
Chrome plating, or chrome plating, is a type of electroplating that involves adding a thin layer of chromium to a metal part to increase its surface hardness or corrosion resistance. Adding a layer of chrome can make the part easier to clean and improve its aesthetics, and nearly all metal parts can be plated with chrome, including metals such as aluminum, stainless steel and titanium.
The chrome plating process typically includes degreasing, manual cleaning and pretreatment of parts before they are placed in the chrome bath. The part must then remain in the tank long enough for the chrome layer to reach the desired thickness. Because the process consumes electricity and involves multiple steps, chrome plating is a relatively expensive finishing process that is not environmentally friendly
Polytetrafluoroethylene (Teflon™) coating
Polytetrafluoroethylene (PTFE) coatings, commonly known as Teflon™, are available in powder and liquid form and are used throughout industry. Some PTFE applications require only one coat, but others require a primer and topcoat to ensure maximum protection. This surface treatment can be applied to a variety of metals, including metals such as steel, aluminum and magnesium.
PTFE-coated parts have a non-stick surface, low coefficient of friction and are highly wear-resistant. Because PTFE coatings have low porosity and low surface energy, coated parts are resistant to water, oil and chemicals. PTFE can also withstand temperatures up to 500°F, is easy to clean, and has excellent electrical insulation and chemical resistance.
Because of its chemical resistance and nonstick properties, PTFE is commonly used to coat fuel lines and to insulate circuit boards in computers, microwave ovens, smartphones and air conditioners. It is also commonly used to coat medical equipment as well as cookware. While PTFE coating processes are popular across industries, they are relatively costly and not as long-lasting as other chemical finishing options.
Electroless Nickel
Electroless nickel plating refers to the addition of a protective layer of nickel alloy on metal parts. In contrast to the electroplating process, which involves an electric current, electroless nickel involves depositing a layer of nickel alloy (usually nickel phosphorus) on the part using a nickel bath and a chemical reducing agent such as sodium hypophosphite. Nickel alloys are deposited evenly, even on complex parts with holes and slots.
Nickel-plated parts have higher resistance to oxygen, carbon dioxide, salt water and hydrogen sulfide corrosion. Nickel-plated parts also have good hardness and wear resistance, and can be made even harder with additional heat treatment. Electroless nickel is compatible with a wide variety of metals, including aluminum, steel and stainless steel.
The process of electroless nickel plating is very challenging. Common problems include build-up of contaminants in the nickel bath, rising phosphorous levels and subsequent reduction in plating rate. Additionally, wrong temperature or pH can cause coating quality issues such as pitting, dullness and roughness. Electroless nickel is not suitable for rough, uneven or poorly finished surfaces, and parts need to be cleaned of oil and dirt before starting the plating process.
The different types of electroless nickel coatings are classified according to the weight percent phosphorus in the alloy. Different levels of phosphorus content also provide different levels of corrosion resistance and hardness:
Low Phosphorus Nickel (2 – 4% Phosphorus): Low Phosphorus electroless nickel deposits have a hardness between 58 and 62 Rc and are very wear resistant. It has a high melting point and has good corrosion resistance under alkaline conditions. Low phosphorus electroless nickel deposits are compressively stressed and are generally more expensive than medium and high phosphorus nickel.
Medium Phosphorus Nickel (5 – 9% Phosphorus): Medium Phosphorus Nickel deposits fall between low phosphorus nickel and high phosphorus nickel. It is corrosion resistant in alkaline and acidic environments and has a fast deposition rate (18 to 25 µm per hour). The coating hardness of medium phosphorus nickel can be any value between 45 and 57 Rc, and the coating can reach 65 to 70 Rc through heat treatment.
High Phosphorus Nickel (>10% Phosphorus): Since the high phosphorous deposits of electroless nickel are amorphous, the parts do not exhibit phase boundaries or grains, which improves their corrosion resistance, making them ideal for use outdoors or in extreme environment. High phosphorus electroless nickel also offers ductility, high thickness and stain resistance, and makes the end product easier to polish or weld.
Galvanized
Galvanizing, or zinc chromate, is a popular chemical finish that protects steel components from moisture and corrosion. Galvanized parts provide longer life, improved aesthetics, and a more uniform appearance. Galvanizing can also change the color of the part to silver blue, yellow, black or green. Another significant benefit of galvanizing is that it protects the surface of the part for a long time: Even if the coating is scratched, the zinc reacts with the atmosphere and oxidizes quickly. However, because zinc is chemically sensitive to acids and bases, galvanizing may not be adequate for parts in wet or extremely wet environments.
Conclusion
Chemical surface treatment options offer a variety of methods to achieve the desired quality and performance level of a part, but not every finishing process is suitable for every material and end use. To determine which chemical surface treatment is right for your part, you need an in-depth understanding of key factors such as how much corrosion, friction and wear resistance the final part needs, the environment in which it will be used, and its desired conductive or insulating properties.
Given the importance of these considerations, it’s worth finding a manufacturing partner to help you choose the right finish and ensure it delivers the best possible quality and cost-efficiency. At AN-Prototype, our expert team of machinists and engineers can provide insight not only into chemical surface treatment processes, but also into material selection, tooling and appropriate CNC technology. If you would like to learn more about the finishing options available for your next CNC machining project, please contact us today.