Anodizing titanium is a complex process, but with the right knowledge and equipment, it can offer significant benefits for a wide range of applications. By understanding the science behind anodizing, choosing the right method, and following best practices, you can achieve great results and enhance the properties of titanium even further. So why not give anodizing titanium a try and see what it can do for your next CNC machining project? With the tips and information in this ultimate guide, you’ll be well on your way to success.
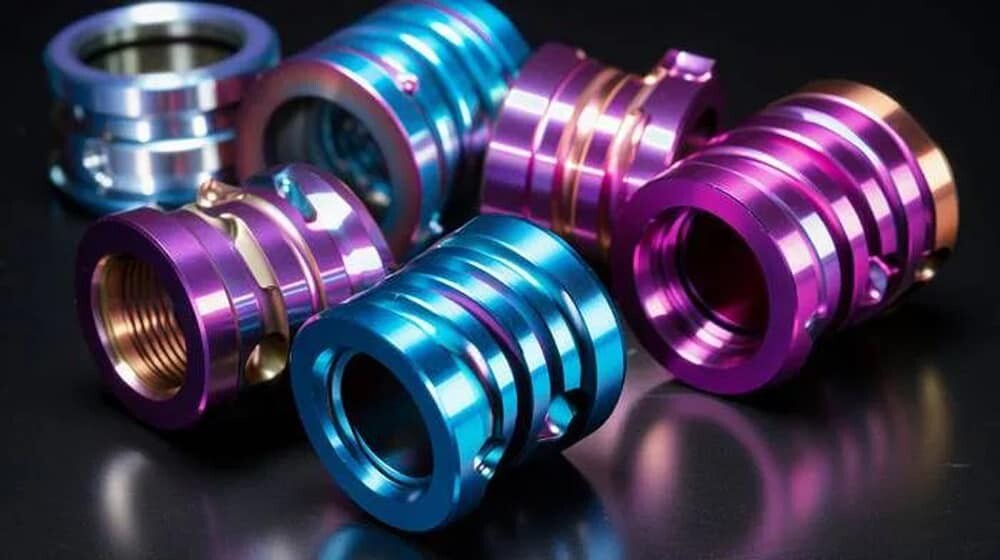
Table of Contents
ToggleWhat is anodized titanium?
Anodized titanium is a process of subjecting titanium to an electrolytic oxidation. This oxidation process creates a protective oxide layer on the surface of the metal, allowing titanium to improve its resistance properties. Anodizing is usually done in sulfuric or phosphoric acid electrolytes, and it creates a protective layer of various colors that can be used for decorative purposes, protective coating that enhances the metal’s properties.
There are a few different types of anodizing methods you can use for titanium. Here are the most common methods:
1. Type II Anodizing – This method is the most common and creates a thin, uniform oxide layer on the surface of the titanium. It’s best for applications where a decorative finish is desired.
2. Type III Anodizing – This method creates a much thicker oxide layer and is best for applications where wear resistance and hardness are important. It’s also known as “hardcoat” anodizing.
3. Hybrid Anodizing – This method combines both Type II and Type III anodizing processes to create a hybrid layer that offers the benefits of both methods.
Step-By-Step Process of Titanium Anodizing
Step 1: Cleaning and Preparation
The first step in the titanium anodizing process is to properly clean and prepare the metal surface. This involves removing any oil, grease, dirt, or other contaminants from the surface using a degreaser or alkaline cleaner. Next, the titanium is rinsed with water to remove any traces of the cleaning solution. This step is important because any residue on the surface can interfere with the anodizing process and affect the quality of the final product.
Step 2: Etching
After cleaning and preparation, the titanium undergoes an etching process. This involves placing the metal in an acid solution, usually a mixture of phosphoric and sulfuric acids, to remove a thin layer of the surface. This creates a micro-roughened surface that’s better suited for anodizing. The etching process also removes any residual contamination that might be hiding in the surface.
Step 3: Anodizing
The next step in the process is anodizing itself. This involves immersing the titanium in an electrolytic solution, usually sulfuric acid, and applying a current to the metal. This causes an oxide layer to grow on the surface, which can be controlled by varying the voltage, current, and time of the process. The thickness and color of the layer can also be controlled by adding pigments or dyes to the solution. The anodizing process can take anywhere from a few minutes to several hours, depending on the desired thickness and color of the layer.
Step 4: Sealing
Once the anodizing process is complete, the oxide layer is porous and vulnerable to moisture and other contaminants. That’s why the final step in the process is sealing. This involves placing the titanium in a hot water or steam bath to close the pores and create a durable, impermeable, and corrosion-resistant oxide layer. The sealing process can also affect the color of the oxide layer, especially in the case of dyed titanium. The final product is a smooth, even, and vibrant surface that’s ideal for a range of applications.
Step 5: Post-Treatment
After the sealing process, the anodized titanium is inspected and tested for defects, thickness, and color consistency. Any irregularities or non-conformities are corrected, and the product is thoroughly cleaned and dried before delivery to the client. The post-treatment step is critical to ensuring the quality and performance of the anodized titanium and ensuring customer satisfaction.
Titanium anodizing is a complex and multi-step process that’s essential for enhancing the durability, wear-resistance, and aesthetic appeal of titanium parts. By following the steps outlined above, CNC machining designers can better understand this important process and ensure the quality, consistency, and reliability of their products. Whether you’re making aerospace components, medical equipment, or custom jewelry, titanium anodizing can help you achieve the desired results and stand out from the competition.
Advantages of Anodized Titanium
Anodized titanium is a versatile material that offers a range of benefits for CNC machining designers. From enhanced durability and corrosion resistance to aesthetic appeal and lightweight properties, anodized titanium can be leveraged to create products that are both functional and visually appealing. As a CNC machining designer, incorporating anodized titanium into your designs can help you create products that are both durable and sustainable, while also adding a touch of sophistication and style to your creations.
1. Enhanced Durability
One of the biggest advantages of anodized titanium is its enhanced durability. The anodization process creates a hard and wear-resistant oxide layer on the surface of titanium, making it more resistant to scratches, dents, and wear and tear. This is particularly useful for products that are subject to rigorous use or exposure to harsh environments, such as industrial machinery, aerospace components, and medical devices.
2. Corrosion Resistance
Another advantage of anodized titanium is its excellent corrosion resistance. The oxide layer created during the anodization process acts as a barrier that protects the underlying titanium from corrosion caused by exposure to moisture, chemicals, and other environmental factors. This makes anodized titanium ideal for products that are used in corrosive environments or are exposed to harsh chemicals, such as marine equipment, chemical processing equipment, and automotive components.
3. Aesthetic Appeal
Anodized titanium offers a wide range of colors and finishes, which can be customized to suit your design requirements. The anodizing process allows for the creation of a range of colors, from vibrant hues to subdued tones, that can be used to enhance the visual appeal of your products. Anodized titanium also offers various finishes, including matte, glossy, and textured, which can be used to add depth and dimension to your designs.
4. Light Weight
Titanium is already known for its lightweight properties, making it an excellent choice for products that require a high strength-to-weight ratio. Anodized titanium is even lighter than regular titanium due to the thin layer of oxide on its surface. This makes it an ideal material for products that require superior strength and durability without adding extra weight, such as sporting goods, electronics, and aerospace components.
5. Environmentally Friendly
Finally, anodized titanium is an environmentally friendly material that is safe for use in various applications. The anodizing process is non-toxic and does not emit any harmful chemicals or vapors into the environment, making it a sustainable and eco-friendly choice. Anodized titanium is also highly recyclable, which reduces its carbon footprint and minimizes waste.
Challenges in Titanium Anodizing
Titanium anodizing is a critical process in CNC machining, and designers must overcome several challenges to achieve high-quality results. From preparing the surface and achieving uniform coating thickness to controlling the color of the finished product, there are several steps that designers can take to overcome these challenges. With a little patience and care, designers can create beautiful anodized titanium components that will last for years to come.
1. Preparing the Surface for Anodizing:The first step in titanium anodizing is preparing the surface. Titanium is known for its ability to form a passive oxide layer, which protects it from corrosion. This can make it difficult to get the anodizing solution to bond with the titanium surface. To overcome this issue, designers should use a vigorous acid wash to remove any passive layer from the surface. This will help the anodizing solution to bond with the titanium surface more effectively.
2. Achieving Uniform Coating Thickness: Achieving uniform coating thickness is a critical aspect of anodizing titanium components. Uniform anodization is necessary to create a consistent and even finish across the entire surface. The surface finish of the component can impact the coating thickness and can lead to variations in the anodizing result. To overcome this challenge, designers should ensure that the surface finish is uniform across the entire component before anodizing. They can achieve this through abrasive blasting or chemical etching.
3. Dealing with High Current Density: Titanium anodizing requires a higher current density than other metals like aluminum. The higher current density can cause localized heating of the component, leading to uneven anodizing. To avoid this, designers should use a pulse anodizing process, which intermittently applies the current to the component. This will help to distribute the heat more evenly and minimize localized overheating. The pulse anodizing process also creates a denser coating that resists wear and tear.
4. Avoiding Contamination: Contaminants on the titanium surface can affect the anodizing process, leading to an uneven or poor finish. Contamination can occur from oils or other substances left on the surface of the component, or from the anodizing solution itself. To overcome this challenge, designers should ensure that the surface is thoroughly cleaned and free of any contaminants before anodizing. They can use a combination of solvents, acid solutions and ultrasonic cleaning to remove any potential contaminants.
5. Controlling the Color of the Finished Product: Titanium anodizing allows for a wide range of color choices, depending on the applied voltage and anodizing time. However, controlling the color can be challenging, and the resulting color can vary even for small variations in the anodizing conditions. One solution to this challenge is to use a computer-controlled process for anodizing. This will allow designers to create precise and uniform colors for the finished product.
Titanium Anodizing Vs. Aluminum Anodizing
Both titanium and aluminum anodizing have their pros and cons. If you’re looking for a material that is durable, corrosion-resistant, and has an attractive finish, titanium is the clear winner. However, if you’re on a tight budget and looking for a simpler anodizing process, aluminum is a good option.
1. Durability: Titanium is known for its strength and durability. It has a higher tensile strength than aluminum, which means it can withstand greater stress without breaking. It is also highly resistant to scratches and abrasions. When anodized, titanium forms a thin, hard oxide layer that further enhances its durability. On the other hand, aluminum is relatively softer than titanium and prone to scratches and dents. When anodized, the oxide layer on aluminum is not as hard as titanium, making it more prone to wear and tear.
2. Corrosion Resistance: Both titanium and aluminum form an oxide layer when anodized, which adds to their corrosion resistance. However, titanium’s oxide layer is denser and thicker than aluminum’s oxide layer. It is also more resistant to acidic and saltwater environments, making it an ideal choice for marine and aerospace applications. Aluminum’s oxide layer, while effective in moderate environments, can degrade quickly in harsh conditions. This makes titanium the clear winner in terms of corrosion resistance.
3. Aesthetic Appeal: Anodizing provides a range of colors and finishes to the surface of the object. While both titanium and aluminum can be anodized in a variety of colors, titanium offers a wider range of colors and finishes. Titanium anodizing can produce vibrant and iridescent colors that are not possible with aluminum anodizing. It can also be polished to a mirror-like finish, creating a premium look and feel. Aluminum anodizing, on the other hand, is ideal for creating a matte finish or a natural metal look.
4. Cost: The cost of anodizing depends on several factors, including the size of the object, the quantity, and the desired finish. Generally, titanium anodizing is more expensive than aluminum anodizing. This is because titanium is a harder and more challenging material to work with than aluminum. It requires specialized equipment and expertise to achieve the desired results. Aluminum anodizing, on the other hand, is a relatively simpler process and can be done at a lower cost.
Applications Of Anodized Titanium Parts
The applications of anodized titanium parts are diverse, ranging from medical devices to aerospace industry, automotive industry, sports equipment, and electronics industry. Companies across different industries are recognizing the benefits of using anodized titanium parts, including high strength-to-weight ratio, excellent corrosion resistance, biocompatibility, and customizable finishes. With its many advantages, it’s no surprise that anodized titanium is becoming an increasingly popular choice of material for CNC machining designers.
1. Medical Devices:
Anodized titanium parts are an ideal choice for medical devices due to their biocompatibility, strength, and corrosion resistance. They are also lightweight and can be easily customized to suit the specific needs of patients. Titanium parts are used for making orthopedic implants, dental implants, pacemakers, and other medical devices.
2. Aerospace Industry:
The aerospace industry has been a significant user of anodized titanium parts for decades. Titanium is a preferred material for aircraft structures due to its high strength-to-weight ratio, corrosion resistance, and ability to withstand high temperatures. Anodized titanium parts are used in aircraft bodies, landing gear, turbine blades, and other critical components.
3. Automotive Industry:
Anodized titanium parts are finding increasing use in the automotive industry. Titanium is being used in making engine components such as valves, retainers, and connecting rods. The use of anodized titanium parts is particularly beneficial in high-performance vehicles, where lightweight and strong materials are essential.
4. Sports Equipment:
Titanium is being used to make sports equipment due to its strength, corrosion resistance, and lightweight properties. Anodized titanium parts are used in making components for bicycles, tennis racquets, golf clubs, and other sporting equipment. In addition, the use of anodized titanium parts in sports equipment has aesthetic and color advantages, providing a durable and colorful finish.
5. Electronics Industry:
Titanium parts are also finding widespread use in the electronics industry. Anodized titanium parts are being used to make electronic components such as mobile phone cases, laptop casings, and other electronic gadgets. The material provides excellent electromagnetic shielding and has a high strength-to-weight ratio, making it ideal for use in these applications.
Trustworthy Anodized Titanium Service Provider
As a designer, you know that precision and durability are key factors when selecting a titanium machining and anodizing service provider. That is why AN-Prototype stands out as a leader in the industry. With advanced CNC capabilities and top-tier anodizing services, we cater to various industries and can handle everything from prototypes to high-volume production. Furthermore, our metal finishing services ensure that the end-products are of top quality. In this blog post, we highlight how AN-Prototype is advancing the world of titanium machining and anodizing.
Advanced CNC Capabilities
At AN-Prototype, we utilize advanced CNC capabilities to ensure high precision in our titanium machining processes. Our state-of-the-art machines allow us to produce complex geometries, intricate shapes, and high-quality finishes. Our machining processes include turning, milling, wire EDM, and grinding. We use only the highest quality titanium alloys in our machining processes to ensure the best possible end-product for our clients.
High-Quality Anodizing Services
One of the most critical factors in titanium machining is the anodizing service that follows it. AN-Prototype’s anodizing service enhances the durability and aesthetics of titanium alloy products. We offer various anodizing processes, including hard anodizing, black anodizing, clear anodizing, and colored anodizing. Our anodizing process also offers excellent corrosion resistance, wear resistance, and scratch resistance. The end-product is not just functional but also visually appealing.
Catering to various Industries
AN-Prototype caters to various industries, including aerospace, medical, automotive, and marine. With our advanced CNC capabilities and high-quality anodizing services, we can make anything from simple parts to complex components. Our titanium machining and anodizing services are ideal for parts that require high precision, corrosion resistance, and wear resistance.
Top-Quality Metal Finishing Services
AN-Prototype also provides top-quality metal finishing services to ensure that the end-products are of the highest quality. Our metal finishing services include polishing, plating, and painting. We select the best finishing method for each project to ensure that the product’s intended function and appearance are achieved. Our metal finishing services can be applied before or after the anodizing process to enhance the end-product’s performance and aesthetics.