CNC machining titanium parts has become increasingly popular in the aerospace, medical, automotive and energy industries. Titanium alloys have many unique properties and are often the best choice for CNC machined parts with special applications. Titanium has an impressive strength-to-weight ratio, being 40% lighter than steel and only 5% weaker. Despite its popularity, titanium is one of the most difficult metals to machine. AN-Prototype specializes in CNC machining titanium services, no matter how challenging your special requirements, we will meet your requirements. We regularly manufacture different types of titanium parts quickly and cost-effectively.
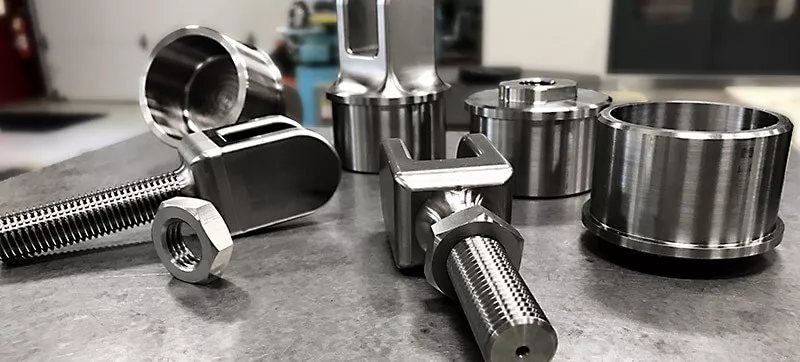
Table of Contents
ToggleWhat is Titanium and its application?
Titanium is one of the most abundant metals on the Earth’s crust, has desirable material properties, is weldable (in an inert atmosphere), and can be CNC machined like stainless steel. Almost all surface finishing services: such as sandblasting, powder coating and electrophoresis will produce good results when applied to titanium parts. However, titanium parts are not always designed and manufactured in the same way as aluminum parts or parts made from lower cost materials. Titanium costs about 10 times that of aluminum 6061, so you need to make sure you get the part done in the first pass. Frustratingly, CNC machining titanium is very challenging.
- Titanium is a biocompatible, non-toxic metal and is corrosion resistant.
- Titanium parts are non-magnetic and have a high strength to weight ratio.
- Titanium has high oxidation resistance.
- Titanium can be easily alloyed with iron, vanadium, aluminum, molybdenum and nickel to produce strong metal parts.
- Titanium is 100% recyclable and is an environmentally friendly metal material.
For these reasons, CNC titanium parts are often used in industries such as aerospace, automotive, and medical.
Aerospace: aircraft engine parts, fuselage parts, rotors, compressor blades, etc. In fact, the aerospace industry drives titanium production: two-thirds of all titanium produced in the world is used in aircraft engines and airframes.
Medical Industry: Titanium parts include surgical implants (such as long-term hip replacements) and instruments. The metal is also used to make items such as wheelchairs and crutches.
Mechanical Properties of Titanium
- Density: 4.50 g/cm3
- Melting point: 1650-1670 °C
- Boiling point: 3287 °C
- Tensile strength:220 MPa
- Modulus of elasticity: 116 GPa
- Shear modulus: 43.0 GPa
- Hardness, Brinell : 70
- Hardness, Vickers : 60
- Elongation at Break : 54%
Types of titanium
Titanium is available in nearly 40 grades, as well as several other alloys. Grades 1 through 4 are considered commercially pure titanium and have varying requirements for ultimate tensile strength. Grade 5 (Ti6Al4V or Ti 6-4) is the most common titanium alloy, containing 6% aluminum and 4% vanadium. Although titanium and its alloys are often grouped together, there are some key differences between them that must be noted before determining the ideal CNC machining method.
Titanium Grades 1-4 – Titanium grades 1 through 4 are considered the purest. These grades are unalloyed and remain in their pristine condition. As the grade increases, the yield strength and tensile strength of titanium increase. This means that grade 2 titanium has greater tensile strength and yield strength than grade 1 titanium, and so on. While grade 2 titanium is not as strong as grade 5 titanium, it is lightweight and has excellent overall corrosion resistance in addition to excellent formability. These grades have a high strength to weight ratio. Additionally, they are lighter than steel.
Titanium Grade 5 – Titanium grade 5, also known as Ti 6-4, or Ti-6AL-4V, or Ti6Al4V, is one of the most widely used titanium alloys in a variety of applications. Titanium grade 5 is the strongest titanium alloy and has good corrosion resistance and weldability. Due to its ability to withstand high and sub-zero temperatures, titanium can be chosen over other metals such as steel for some applications. Compared with grade 2 titanium, it has higher temperature resistance. This is why this grade of alloy is most commonly used in chemical processing, medical, aerospace, marine and other applications.
Titanium Grade 9 – Grade 9 titanium alloy is known for its high strength. Its tensile strength is higher than that of pure grade 2 titanium alloys. This better strength at both room and elevated temperatures makes this grade of alloy more popular in a variety of applications. This alloy grade is also known as Ti-3AL-2.5V. The weldability of grade 9 titanium alloy is better than that of grade 5 titanium alloy.
Why Choose CNC Machining Titanium?
For the most accurate and affordable titanium parts, CNC machining is almost always the best option. Let’s recognize the pitfalls of other processes for making titanium parts.
Cast Titanium Parts: Rapid manufacturers rarely make titanium parts by casting. This is because heated titanium reacts violently with oxygen, and many foundry refractories contain trace amounts of oxygen.
Stamped Graphite Casting Titanium Parts: The solution is to use Stamped Graphite Casting (using Oxygen Free Graphite Casting), but this produces very rough surface textured parts that are not suitable for most medical, aerospace and industrial applications. Titanium parts can also be made by lost wax casting, but this requires a vacuum chamber.
3D Printing Titanium Parts: A newer option is to use additive manufacturing for titanium parts. A few 3D printing technologies such as Selective Laser Melting (SLM), Electron Beam Melting (EBM) and Direct Energy Deposition (DED) can process titanium 3D printing materials. However, these 3D printing systems are expensive, and many industries have yet to certify 3D printed titanium for safety-critical end-use parts.
It can be seen that compared with other manufacturing processes, CNC machining is a precise, safe, versatile and economical method of manufacturing titanium parts.
The Challenges of CNC Machining Titanium
There are many challenges and problems in traditional titanium CNC milling. By understanding what these challenges are, metallurgists and machinists can find machining solutions that produce high-quality machined titanium parts.
Heat Accumulation
One of the biggest hurdles in CNC machining titanium is keeping everything cool. Titanium’s low thermal conductivity allows metal workpieces to quickly build up heat at the machining location. This increases the wear of the machining tool and creates a secondary effect of titanium alloy hardening which further aggravates tool wear. If not addressed, this can have an adverse effect on the quality of the cut surface.
"Fudge" Properties
Titanium’s low modulus of elasticity causes it to have a “sticky” effect when CNC machining and can cause severe chatter. This can cause cutting titanium chips to stick to the tool. These obstacles further increase tool wear and affect finished surface quality.
Elastic Deformation
The elastic behavior of titanium can also cause the workpiece to be displaced by elastic deformation in the unsupported part during CNC machining. The part bends due to the force generated by the cutting tool and then returns to its normal position after the cutting tool has passed, resulting in larger tolerances in the final part manufactured.
3 Helpful Tips for CNC Machining Titanium
The challenges of CNC machining titanium are enough to make many fast fabricators wary of manufacturing this advanced material. But its outstanding performance means that more and more product designers are seeking high-quality titanium parts. Fortunately, the expert machinists and tool suppliers at AN-Prototype have figured out a few key ways to make titanium CNC machining at least a little easier.
Tip 1 - Use the right tools
With the increasing popularity of titanium parts, tool designers are coming up with unique solutions to improve the machinability of titanium. Advanced tool materials, such as heat-resistant titanium aluminum nitride (TiAlN) or titanium carbonitride (TiCN) coated tools, can extend tool life. At the same time, tools with uneven spacing between cutting edges disrupt constructive interference that causes tool chatter.
In general, machinists should choose high-quality tools designed specifically for titanium, and dull tools should be inspected and replaced frequently. Also consider using a smaller diameter tool with more cutting edges. This helps maintain metal removal rates while reducing heat buildup.
Tip 2 - Keep the workpiece and CNC machine stationary
It is easy to cause tool chatter during CNC machining of titanium, so do anything you can do to reduce the vibration to make CNC machining titanium easier. Make sure the parts are well supported and fixed to prevent the workpiece from deforming and lay out a high quality CNC machine. You might even consider using shorter cutting tools to reduce tool deflection.
Tip 3 - Adjusting CNC Milling, Turning Parameters
CNC machining titanium requires careful temperature management. One of the most obvious ways to keep your workpiece and tool cool is to apply a consistent high-pressure coolant directly to the cutting area. Ejecting chips away from the cutting zone also prevents them from sticking to the machining tool.
At the same time, it is also important to pay special attention to feed rate, spindle speed and chip load. This means protecting tools and equipment from excessive stress while avoiding staying in the same position for too long.
CNC Machining Titanium Services
AN-Prototype offers a complete titanium CNC machining service to manufacture custom titanium parts in complex organic geometries with tight tolerances in grade 1 titanium, grade 2 titanium and grade 5 titanium. AN-Prototype guarantees consistent quality and fast turnaround time at always competitive prices. You can apply up to 6 different post-treatment/surface finishing options including sandblasting, powder coating, smoothing and polishing, electrophoresis, anodizing and more.