Anodizing aluminum is an electrochemical process that produces a wear-resistant, corrosion-resistant aluminum oxide coating on the surface of aluminum parts. Aluminum anodizing is an electrolytic process carried out in an electrolyte such as dilute sulfuric acid. Current is passed through the part, causing negatively charged oxygen ions in the electrolyte to be attracted to positively charged aluminum atoms created on the metal surface. The oxyanions react with the aluminum cations to form a strongly adherent aluminum oxide layer. There are three different anodizing processes: Type I (chromic acid anodizing), type II (sulfuric acid anodizing) and type III (hard coat anodizing). The anodizing process is applicable to a wide variety of materials, but the most important and most commonly used material is aluminum. Other less common types are magnesium anodizing and titanium anodizing.
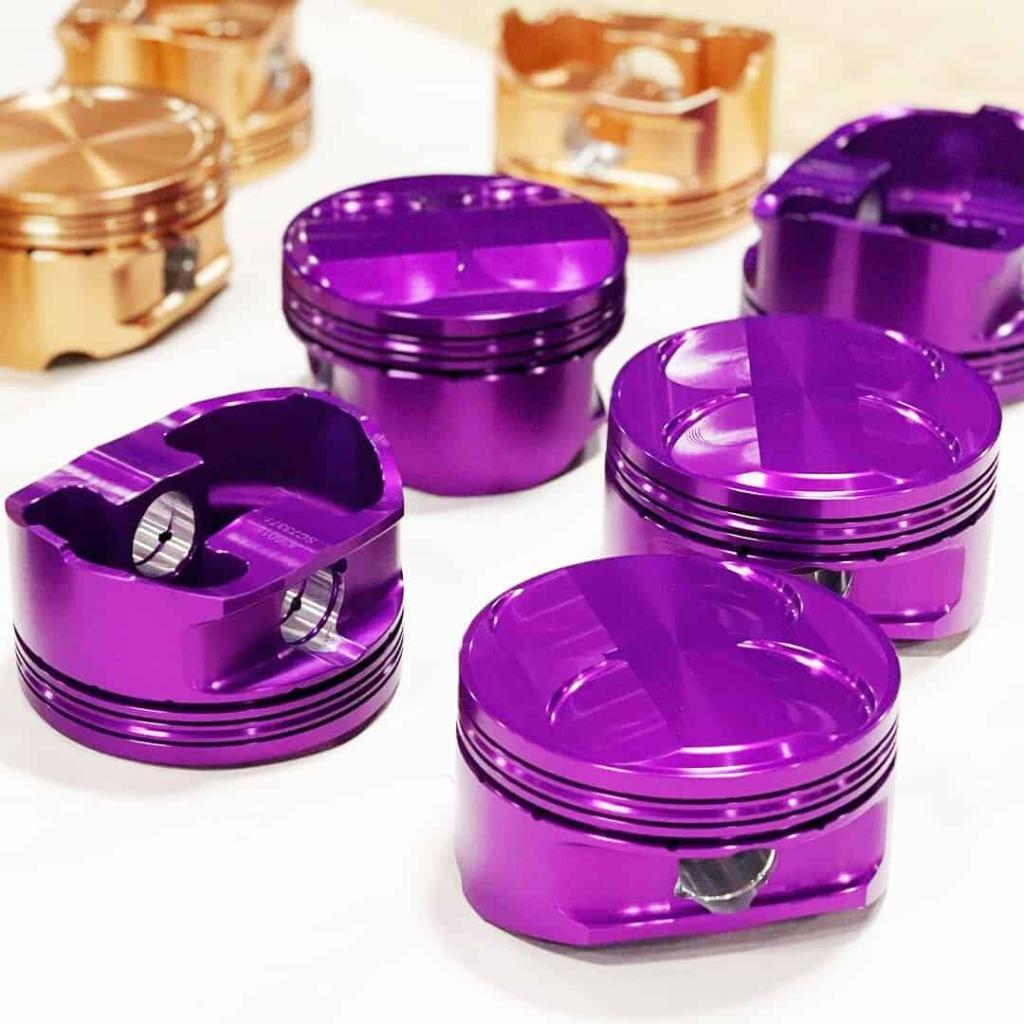
Table of Contents
ToggleAnodized Aluminum
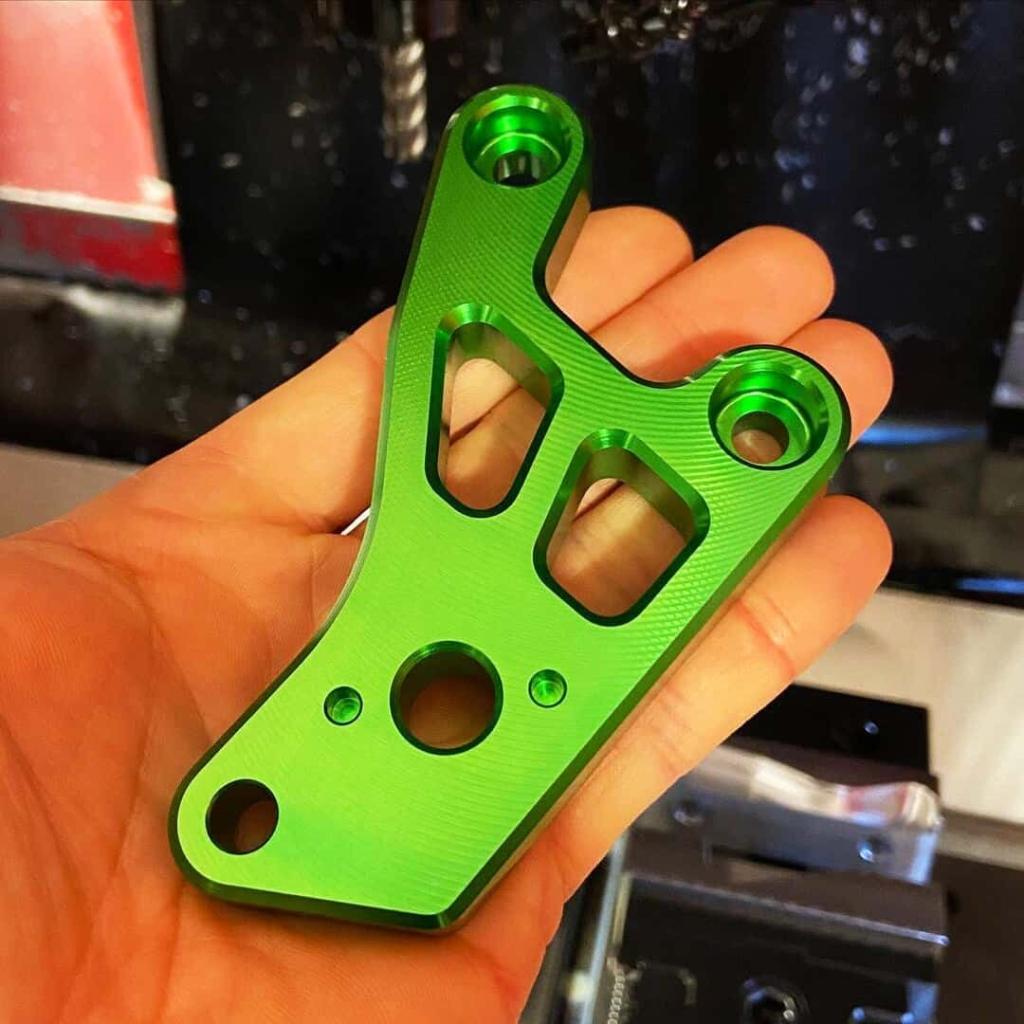
Anodized Magnesium
Anodizing is a porous structure that grows from the base aluminum and absorbs colored dyes very well. AN-Prototype uses standard organic dyes for black, blue, red, gold and small batches of green and gray to create anodized aluminum parts in any color given your Pantograph number. Sealing is required after any colored anodizing to retain the color.
Anodized aluminum is an excellent choice when you need aluminum prototypes or low-volume aluminum parts with superior mechanical properties and professional aesthetic designs. The anodizing process forms a layer of oxide on metal parts, which effectively improves corrosion resistance, also enhances visual quality and protects the surface from scratches.
What is the purpose of anodizing aluminum?
The purpose of anodizing aluminum is to increase its wear and corrosion resistance. Aluminum is a popular metal used to make everything from electronics to car parts because it is strong and lightweight. However, aluminum is also very susceptible to corrosion and wear when the corrosion potential of the environment increases, such as exposure to seawater and other extreme conditions. To prevent this, manufacturers often anodize the metal, creating a thin oxide layer that protects against corrosion and wear.
Where is anodized aluminum used?
Anodized aluminum is suitable anywhere aluminum components may be exposed to corrosive or wear-resistant applications, such as automotive parts, bicycles and outdoor products. Anodized aluminum can be easily stained for a scratch-resistant colored finish. Therefore, it is used in many consumer products to improve their appearance and increase their durability. For example, the casing of the Apple mobile phone uses an anodic oxidation process. Anodizing also turns aluminum into an insulator because the oxide coating does not conduct electricity.
Surface treatment before anodizing aluminum
Aluminum parts are cleaned before anodizing. This is important to remove impurities that can hinder the process. Mechanical finishing techniques are used where necessary. The etching process alone is not enough to correct existing surface defects on aluminum parts, such as scratches and dents. If these marks are evident on the surface of the aluminum part, you may wish to use mechanical finishing techniques such as grinding, polishing and sandblasting.
Be careful with your packaging. Before sending parts for anodizing, make sure you pack them dent-proof and well-cushioned. Also, avoid applying tape directly to the surface of the aluminum part to be anodized. Make sure your parts are properly cleaned and degreased. Watch out for uncleaned swarf on blind holes, fingerprints on surfaces (avoid handling parts with bare hands!), and oil residue from the manufacturing process.
How to anodize aluminum parts?
The working principle of anodized aluminum parts involves inducing oxidation of the aluminum by immersing the aluminum part in a conductive acidic electrolyte solution, which releases oxygen ions. This method utilizes an anodic film for aesthetic effect. To gain a better understanding of the process of anodizing aluminum parts, there are 4 main steps involved:
Step 1: Preprocessing
The pretreatment process involves achieving a visible surface finish and a clean workpiece.
Cleaning: Pre-processing cleaning is important to remove grease, oil and other impurities from previous manufacturing processes such as extrusion or CNC aluminum machining to avoid impurities and inconsistencies in the finished part.
Etching: The surface finish of the part before anodizing is important as it will determine the quality of the final result. Etching can be used to adjust the desired surface finish, correcting minor imperfections on the surface in preparation for anodizing.
Step 2: Anodizing
After the surface is prepared, the part goes through an anodizing step, dipping into a bath of sulfuric acid electrolyte solution (this may vary depending on the type of anodizing process chosen). Electrolyte solution contains many positive and negative ions and is a conductive solution.
Positive ions are attracted to the negative plate, and negative ions are attracted to the positive plate. The current in the circuit causes it. Negative ions attract the aluminum part, the positive electrode. Aluminum parts will be used as anodes.
At the same time, a cathode is installed in the cell, allowing current to actively pass through the system and induce the release of oxygen ions in the electrolytic solution. This process will create aluminum oxide in the substrate, also known as a barrier layer. But it is rougher than aluminum surface.
Step 3: Coloring
The anodic coating formed on the surface layer is porous due to its structure, which adds color to the part. Various methods of adding color to anodized parts include dipping them in dyes or dissolved metal salts. The process can achieve black, blue, purple, red, gold, yellow and other finishes.
Step 4: Seal
To seal the porous surface created during the anodizing process and provide a uniform surface, the part needs to go through a final step where it is immersed in a nickel acetate solution. Sealing ensures long-lasting color and prevents further corrosion of anodized parts.
Different Types of Anodizing Aluminum Processes
There are three main types of anodizing processes for aluminum parts, leading to the different finishes and appearances we see.
Type I Chromate Anodizing
Type I chromic acid anodizing uses a chromic acid solution to form a thin coating (0.5 to 2.5 microns) on aluminum parts. Chromate anodizing produces the thinnest coating and the least color absorption of the three main anodizing types. Although the coating is relatively thin, it protects aluminum parts from corrosion and is an effective first coat for powder-coated or painted finishes.
Type II sulfuric acid anodizing
Type II anodizing is the most common method of anodizing aluminum parts. It produces anodized layers from 2.5 to 25 microns. The porous nature of the process is ideal for dye absorption. Type II is not suitable for aluminum parts with tight tolerances.
Type III Hard Anodizing (Hard Anodizing)
Type III hard anodizing is also done in a sulfuric acid solution. However, the resulting coating is thicker and denser than ordinary sulfuric acid anodizing. Coatings on Type III alumina are fairly hard, and differences in the thickness of the hard coating can alter the surface appearance of the substrate. It is used in harsh applications requiring excellent wear and corrosion resistance, such as medical equipment, etc.
Which type of anodizing is right for you?
Choosing the most suitable type of anodizing and understanding how anodizing works is not easy. You should choose an anodizing process based on the various applications for your aluminum parts. A qualified rapid manufacturing company can advise on which type of anodizing is best for your project. You can choose the best anodized aluminum parts by comparing different types of anodizing.
Type 1 anodizing has specific properties such as good corrosion resistance and uses chromic acid to form a thin layer on the surface of aluminum parts. Type 1 is for aircraft components.
Type II anodizing is primarily used for most applications. Type II uses sulfuric acid instead of chromic acid to create a thick anodized layer on the part. Type II has moderate wear resistance and uses sulfuric acid to form a thicker layer on the surface of the aluminum part.
Type III anodizing is best for parts that can withstand chemical exposure and high temperatures. Type III has the same characteristics as type II, but with some differences in outcome. Type III produces a layer of corrosion that is used to create strong aluminum parts.
Benefits of Anodized Aluminum Parts
There are many advantages to anodizing aluminum parts, here are some reasons why you might want to:
Aesthetics – Anodized parts add a touch of elegance and enhance the overall surface finish and visual appeal of the part.
Durability – The entire process of anodizing improves the overall corrosion and wear resistance of the part, which greatly contributes to extending the life of the aluminum part.
Ease of Maintenance – The corrosion and wear resistance of anodized aluminum makes parts less prone to dents and wear.
Color Stability – Unlike other plating methods used in the industry, anodized parts will not flake due to their dense structure.
Economical – Aluminum anodizing is inexpensive and allows for a desirable finish and impressive surface properties.
Insulating Properties – The outer anodized layer of anodized aluminum parts is insulating and has low electrical conductivity. This is a big reason why aluminum is chosen for anodized parts.
Anodized Aluminum Design Tips and Considerations
Size Compensation
Remember that you will need to compensate for anodization thickness when obtaining final part dimensions and feature tolerance assignments.
Hardness requirements
Note your application and its tensile strength requirements to understand the hardness you need to achieve in your part design.
Color Matching
Manage your expectations when setting your desired color, as different metals and alloys react with different stain compounds and tinting parameters.
Combination paint
Anodized parts can also undergo secondary coating processes such as painting and Teflon dipping to further enhance their corrosion resistance and structural integrity.
Conductivity
Testing for conductivity is an easy way to check the anodization of aluminum parts. It can check the conductivity of a surface using a digital multimeter. The anode layer can be a good insulator and can be coated with a clear chemical conversion coating in some areas.
Applications of Anodized Aluminum
Anodized aluminum parts have excellent performance in mechanical and aesthetic properties, and are used in almost all walks of life:
- Aerospace
- Defense industry
- Medical industry
- Automobile industry
- Consumer electronics products
- Achitechive
- Prototyping and Product Development
- Household goods etc.
Conclusion
Anodizing is an important process in the manufacture of aluminum parts that involves immersing aluminum parts in electrolytic solutions and chemical baths. It is widely used in many industries and proven to help provide a safe lifestyle. The cost and complexity of the process varies, but it ensures you a better, high-quality end product.
At AN-Prototype, we provide professional aluminum anodizing services that bring you the best value through high-quality workmanship, fast turnaround times, and competitive pricing. If you have any quotes or projects to review, please feel free to contact us.