Injection Mold Making
AN-Prototype has the ability to manufacture precision molds to obtain custom outstanding high-quality injection molded plastic parts, fulfilling its commitment to quality, fast delivery and competitive prices.
- ISO9001&ISO13485 Certified
- Tolerances Up to ±0.002mm
- Professional DFM Report
- Free Mold Flow Analysis

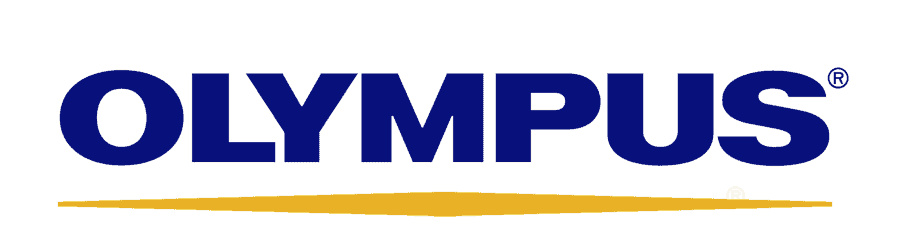
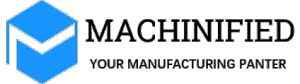
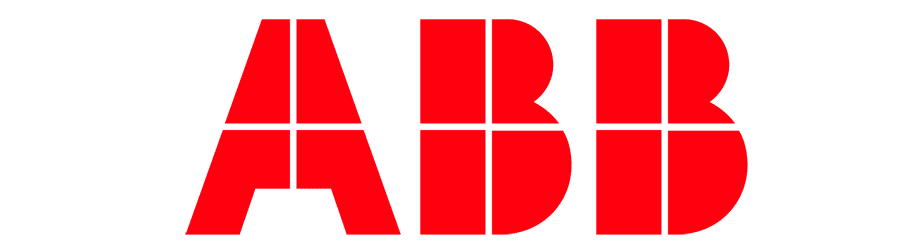

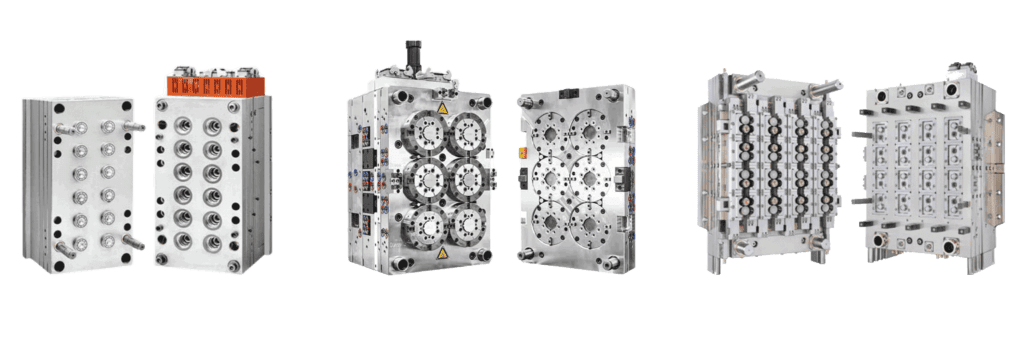
Start Your Injection Molding Quotion
STEP | STP | SLDPRT | IGS | X_T | PDF files
- All uploads are secure and confidential.
Make Perfect Mold Toolings For Better Production
Manufacture your injection molded parts with state-of-the-art processes. At AN-Prototype, we are fully capable of creating custom injection mold toolings that guarantee your project a great success. We know enough about injection molding to understand the uniqueness of your project and then manufacture precise plastic injection molds to your specifications. AN-Prototype’s professional technicians can handle all the complex issues involved in the mold production process, not limited to the structure, material, surface treatment, quality, delivery and ultra-high-volume manufacturing of parts.
In the mid-1950s, the invention of the great reciprocating screw provided inspiration for the manufacture of plastic parts, solved the problem of uneven heating of plastics when heated, and opened up new horizons for mass production. Plastic injection molding is a process used to create large quantities of custom plastic parts. Applications range from complex aircraft components to simple products such as children’s toys.
With skilled mold designers, software technology and expensive CNC machines, AN-Prototype manufactures plastic injection molds for the production of high-quality molded plastic parts. Our injection molding experts look forward to working with you on your mold making projects to create a solid foundation for manufacturing custom plastic parts. If you are looking for plastic injection mold suppliers, we can meet your needs.
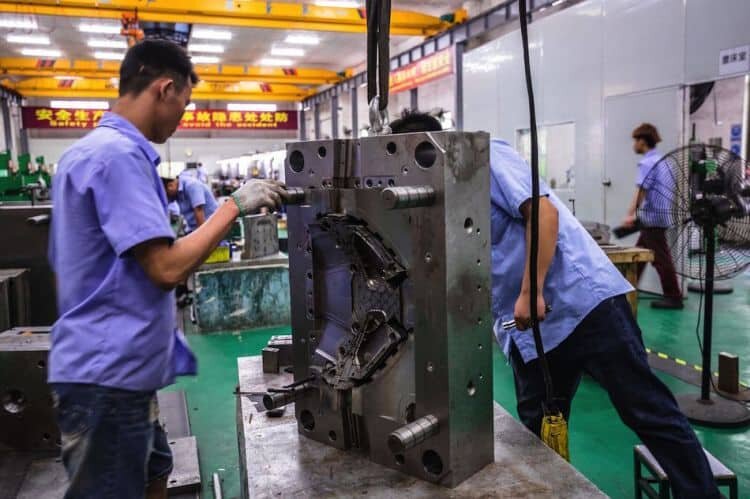
Types of Plastic Injection Mold tooling
Injection molds can be divided into injection molding prototypes and production molds according to their purposes.Injection molding prototypes are easy to get design feedback and verification through high-quality prototype molds. Create low-volume custom plastic molded parts from outstanding injection molded prototypes. AN-Prototype excels at making prototype molds within days to ensure you complete functional testing and verify market interest. General prototype tooling uses affordable aluminum as a raw material, helping you reduce financial risk before full-scale production.Production molds are high-quality production molds for mass production of plastic parts. Our production tooling is made of high-strength, durable steel and is suitable for producing hundreds of thousands of parts.
According to the structure of injection mold tools, it can be divided into single-cavity mold, multi-cavity mold, Stack Mold and 2K injection mold.
Single-Cavity Mold
Cost-effective single-cavity injection molds are ideal for low-volume manufacturing of plastic parts.
Multi-Cavity Mold
Multi-cavity molds can create high volumes of plastic molded parts, ensuring more efficient use of cycle time while reducing cost per part.
Stack Mold
Increase the throughput of your injection molding process and reduce overall part cost with innovative stack molds that enable multi-component assemblies in one pass.
2K Injection Mold
2K injection molds can make plastic parts of two different materials, seamlessly combining soft and hard plastics into one product. Consolidate manufacturing and assembly into one molding process for cost savings.
Mold Making Processes
DFM
Once the mold order is confirmed, AN-Prototype will start a preliminary analysis of the design to understand part lines, gate locations, etc.
Mold design and mold flow analysis
The next step is to use predictive modeling software to understand how the molten material will behave as it enters the mold to further improve the mold tooling design.
CNC Machining and EDM
AN-Prototype uses precision CNC machines to manufacture the first batch of molds, and according to customer-specified plastic, steel, aluminum and other materials.
T1 sample
The newly made mold started with a T1 sample to get a clear idea of whether it will suit your final molded part.
Improvement if necessary
Based on the analysis of the T1 sample, we review the mold design and make any necessary adjustments.
Commence production and shipping
We manufacture molds to final specifications and then ship them to customers.
How is Plastic Injection Mold Made?
Injection mold tools are mainly manufactured by two methods: CNC machining and electrical discharge machining (EDM).
CNC Machining Mold Tooling
In traditional form, standard mold tooling requires manual use of lathes, mills and drills. With advanced technology, CNC machining has become the main means of making more complex and precise molds.
The mold’s core and cavity are machined from a prepared block of steel, aluminum, or other hard metal, and the process begins with rough CNC machining, using larger cutting tools to cut out rough outlines. Moldmakers generally use less accurate (and therefore less expensive) CNC machines for rough machining before moving the mold blanks to high-precision machines. Then according to the design of the mold, the mold is further finely processed.
At the same time, the copper block was also machined at the same time as the steel to ensure that EDM electrodes could be used immediately for further machining of the mold.
Rich Experience in Mold Manufacturing
Electrical Discharge Machining for Mold Making
After CNC machining of the mold parts, the final touches are applied to the geometry. This requires electrical discharge machining (EDM) to achieve certain geometries that CNC mills cannot create.
Electrical discharge machining (EDM) has been widely used in mold making. EDM is a process of obtaining the desired shape by using electrodes made of graphite or copper. It is then mounted in an EDM machine and positioned over the workpiece immersed in a dielectric fluid. The advantage of the EDM process is that it allows pre-hardened mold forming and does not require additional heat treatment. For example, wire EDM is used to cut gear teeth with sharp interior corners and square holes. Cavities, cores, tappets, slides and inserts are subjected to a sedimentation discharge machining process using CNC-machined copper electrodes. The resulting fine EDM finish can be used as a final part finish without any polishing of the mold cavity.
Materials for Injection Mold Tooling
The material used in the mold determines its service life and the quality of the injection molded part. We offer several grades of material for injection molds used in different stages of product development. Our professionals select suitable materials to achieve different levels of dimensional accuracy and aesthetic quality. We also provide professional advice on mold materials.
Tool Steel
Manufactures high tolerance CNC machined molds, most commonly used materials include tool steel.
Type: P20, H13, S7, NAK80, S136, S136H, 718, 718H, 738
Stainless Steel
Injection molds are only used for mass production and are usually made of expensive steel and stainless steel.
Type: 420, NAK80, S136, 316L, 316, 301, 303, 304
Aluminum
Aluminum molds cost significantly less than tool steel and stainless steel. Aluminum molds offer faster cycles and quick turnaround for low-volume manufacturing.
Type: 6061, 5052, 7075
What is Plastic Injection Molding
A single plastic injection mold can have one cavity, producing one part at a time, or multiple cavities, for very high-volume molds such as bottle cap molds, can have more than 100 cavities.Plastic injection molds consist of two main parts: the cavity part of the mold (Part A) and the ejection part of the mold (Part B). These mold halves are designed to work together as follows:
Injection Molding Process
- Plastic resin from the molding machine enters through the "gate" on the A half.
- The sprue bushing tightly seals the nozzle of the injection barrel of the molding machine. This allows molten plastic to flow from the barrel into the mold (or "cavity").
- The sprue bushing guides the molten plastic through channels (called "runners") machined into the surfaces of the A and B halves of the mold.
- Molten plastic flows through the runner and into one or more dedicated gates and into the cavity to form the desired part.
- Molds are usually designed so that the molded part will reliably remain on the B half of the mold when opened. Runners and sprues are pulled from the A half. When the molded part is ejected from the B half, it falls freely.
Single-Cavity vs Multi-cavity Injection Molding
Injection molding is one of the most widely used methods in the manufacture of plastic parts today, enabling the cost-effective manufacture of identical parts on a large scale. It is often preferred over other manufacturing methods, including CNC machining, polyurethane casting, for high-volume manufacturing of plastic parts.
Multi-Cavity Mold
Single-cavity or multi-cavity molds are the two most widely used molds in injection molding. Although both single-cavity and multi-cavity injection molding processes require the same basic operations to be performed in the same time sequence, the two processes are often used to meet different needs or timing requirements and are therefore rarely interchangeable. Choosing whether to use a single-cavity or multi-cavity injection mold is critical to the success of your project.
Choose between a single-cavity mold or a multi-cavity mold
Choosing whether a single-cavity mold or a multi-cavity mold is best for a particular project is often more complicated than one might think. In general, the choice between a single-cavity mold or a multi-cavity mold depends on the time frame and needs. Multi-cavity molds are often a better choice when many identical parts are required within a set amount of time. Multi-cavity molds allow manufacturers to make more parts faster—a clear advantage of using multiple cavities at the same time.
However, multi-cavity molds are not always the best fit for a particular project. Multi-cavity molds require a larger upfront investment than single-cavity molds. Manufacturing multi-cavity molds is more expensive because they require more material, labor and energy than single-cavity molds. While the investment in multi-cavity injection molds will certainly pay off if parts are being produced in high volumes, it may make more sense to opt for a single-cavity mold when producing small batches.
Designed with the right mold in mind
It is always wise to know your market and gain a solid understanding of your product needs so you can design and manufacture to minimize costs. This is especially true when it comes to injection molding. Given the time and substantial cost involved in creating molds, it is critical for product teams to conduct due diligence and select the type of mold that best fits the product and market needs.
Fortunately, an experienced design partner like AN-Prototype can help make these decisions easier for you. We are experts in the perfect mold creation process as well as design for manufacturing (DFM) principles. The following are the advantages of AN-Prototype in manufacturing mold tools. If you’re ready to get started, contact us today to learn more about our injection molding services.
Trusted Injection Molding Service Company
Why Choose Custom Injection Molding Services From AN-Prototype
Maximum Part Size
1200×1000×500 mm
47.2×39.4×19.7 in.
Minimum Part Size
1×1×1 mm
0.039×0.039×0.039 in.
Mold Cavity Tolerances
+/- 0.05 mm
+/- 0.002 in.
Part to Part Repeatability
+/- 0.1 mm
+/- 0.0039 in.
Secondary Operations
Mold texturing, pad printing, laser engraving, threaded inserts and basic assembly.
Inspection and Certification Options
First Article Inspection,
ISO 9001, ISO 13485
Start your next injection molding project with AN-Prototype
If you don’t want to do project management of all these steps yourself, the team at AN-Prototype can help!Every AN-Prototype injection molding quote comes with a free DFM report and competitive pricing. Once your order begins, our team of project managers and quality engineers will ensure that you receive fully inspected, high-quality parts and deliver them on time according to our fast production schedule.
Gallery of Injection Mold Tooling
Our Happy Clients!
“My experience working with AN-Prototype has been nothing but great. Their communication is exceptional, and Michin was always available to answer any questions I had. The finished products we receive are of the highest quality, and meet expectations. What really stands is the great service I always receive from Michin. He’s always committed to ensuring we were satisfied. Overall, I would highly recommend AN-Prototype and Michin for anyone looking for a reliable and supplier..”
“Even for a complex 5 axis CNC machined part we got very good results from AN-Prototype. We did a lot of projects with AN-Prototype during the last 2 years and they always did an outstanding job – high quality (I can also recommend their rapid tooling service and anodizing), reliable, extremely fast and perfect communication. I highly appreciate working with Davide and Vivian and already recommended them to many of our partners..”
“Happy with communication that give me confidence to choose AN-Prototype. Project manager understood what I needed and offered solutions to solve my problem. The project manager is very positive for me to help overcome some frustrations I had. Delivered the prototype products as promised. Very grateful for the personalized service, and, I am already a returning customer. “